3D printing vocabulary
3D model
The 3D model is the three-dimensional "drawing" of a part. This 3D model can be in OBJ, 3MF, STL, etc. format. This format will be interpreted by a slicing software to be readable by a 3D printer by converting it into a G-code file format.
3D printer
A 3D printer is a machine designed to manufacture 3-dimensional parts by depositing successive layers of melting material (thermoplastic, metal, ceramic, etc.). It is a generic term that covers a large number of very distinct technologies such as FDM, SLS, SLM, SLA printers, etc.
3MF - 3D Manufacturing Format
The 3MF, or 3D Manufacturing Format, is a file format dedicated to 3D printing. It was developed by Microsoft and, like the AMF file format, aims to be an alternative to the STL file format. The 3MF file format is based on the standard, standalone XML (human readable) file format and contains the essential data required by additive manufacturing processes.
3MF format files represent 3D models, they contain all the data that make up the 3D model in order to describe it fully (shape, materials, colors, printing media, etc.).
Pam technology is compatible with 3MF format files.
ABS - Material
ABS is a standard thermoplastic widely used in 3D printing. It is resistant to impact and has a good thermal stability to high and low temperatures. ABS has all the qualities required for 3D printing.
It has a good dimensional stability and is ideal for the manufacture of technical components.
Its median viscosity provides a good performance during its implementation.
ABS/PC - Material
The Acrylonitrile-Butadiene-Styrene-Polycarbonate blend (ABS-PC ) combines the properties of ABS and PC, in other words, the high processing capacity of ABS with excellent mechanical properties, resistance to heat and impact, from the PC. The level of the two components affects the heat resistance. This blend is used in enclosures for professional machines, electrical applications, dashboards, hubcaps, etc.
ADD-ON
An add-on is a feature that is added to existing software. The principle is to provide application overlayers that meet a specific need.
Pollen AM has developed add-ons to make the Cura slicer compatible with Pam technology. These are available for download to all Pam users.
Additive Manufacturing
Additive manufacturing (or 3D printing) is opposed to subtractive manufacturing where material is removed to achieve the desired shape. In additive manufacturing, parts are built by adding successive layers of material.
ALM - Additive Layer Manufacturing
ALM is an additive layer manufacturing process allowing the construction of 3-dimensional parts and offering great flexibility both from an application point of view and in terms of usable materials.
Pam technology is an ALM process.
AMF - Additive Manufacturing File Format
This is a file format dedicated to additive manufacturing introduced in 2011 by the International Organization for Standardization (ASTM). It is intended to replace the STL file format.
The AMF, or Additive Manufacturing File Format, is a native file format for additive manufacturing; it uses an XML (human-readable) format with a hierarchy of five elements: materials, textures, constellations (set of objects) and metadata. In all technical aspects, it is superior to the STL file format.
Pam technology is compatible with AMF format files.
ASA - Material
ASA polymers are styrenic materials and feature high surface quality, good impact strength, chemicals, UV and heat resistance. For these reasons, ASA is used as the material of choice for exterior applications. This material can be easier to 3D print than ABS.
Mainly used in the automotive market for exterior applications, household applications, gardening equipment, etc.
Axis
To build an object in volume, a 3D printer, be it Cartesian, Delta or polar, is used in relation to three orthonormal AXES X (abscissa axis) / Y (ordinate axis) / Z (depth axis).
Bed - Heating build plate
In 3D printing, the bed designates the manufacturing platform or the build plate.
The Pam 3D printers have a heating build plate, capable of heating up to 150°C.
Belt
Belt allows on 3D printers and in Pam systems to transfer the movement of the displacement motors to the printing build plate.
Pam 3D printers are based on Delta type printers and have 3 belt to transfer the mouves in 3-dimensions.
Binder - PIM
In the context of PiM, a binder is a mixture of thermoplastic, plasticizers, waxes and wetting agents, with the surfactant giving plastic behaviour to the powders. Pam Series MC is a 3D printer capable of printing PiM feedstocks (ceramics & metals).
Blender
It is a free and open source 3D modelling software.
The Pam technology, agnostic towards 3D modelling software, is compatible with the main CAO software such as Blender / 3D Slash / Clara.iow / selfcad.com / SketchUp / Blender / DesignSpark / LibreCAD / Meshmixer / nanoCAD / FreeCAD / Sculptris / 3ds Max / nanoCAD / Onshape / Rhino3D / ZBrush / AutoCAD / CATIA / Fusion 360 / Siemens NX, etc.
Bridge
A bridge is a part of the printed part that is suspended, cantilevered, for which no support is generated.
Brims
This is a gripping sacrificial structure that allows the addition of thin edges around the part to be printed, widening the first print layers and creating a larger gripping surface between the model and the build plate. Particularly useful for parts with "islands" ( thin contact points with the build plate), it requires little material and is very easy to remove. This has the advantage of reducing the effects of warping.
Don't confuse the Brim with the raft.
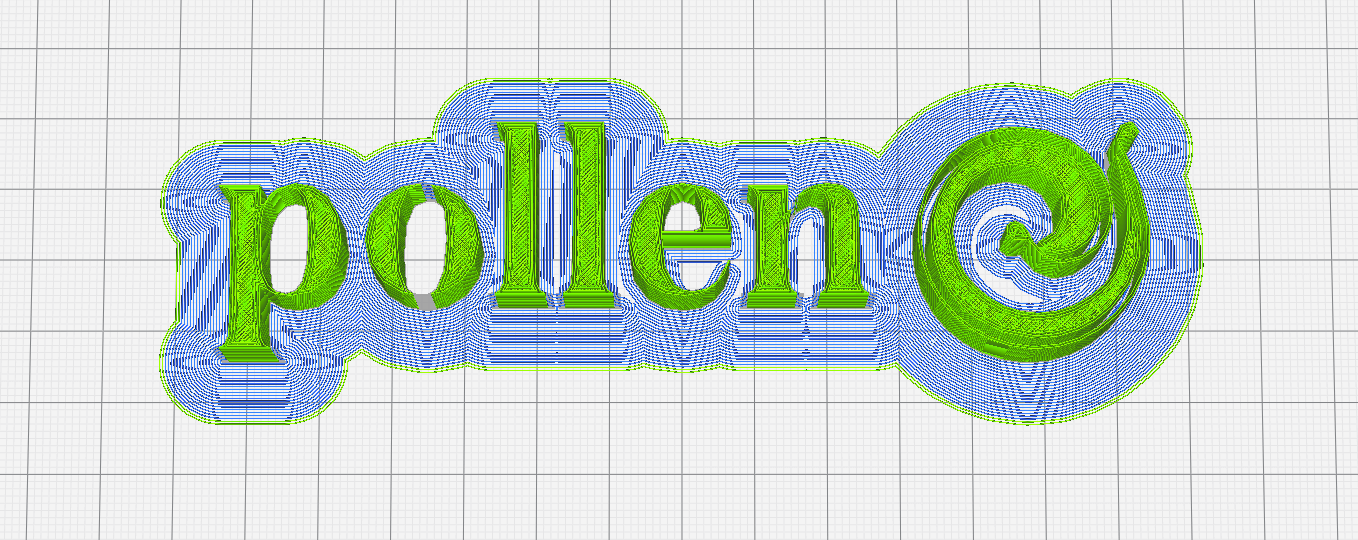
Build plate
Support on which the material in the molten phase will be deposited layer by layer allowing the construction of the workpiece to be printed.
The build plate of the Pam printers is heated, several media are available such as the resin build plate and the micro-perforated resin build plate. It is also possible to add its specific adhesion films to develop an omtilised adhesion between the part being produced and the build plate.
Build plate calibration
Calibrating the build plate is an important step in ensuring the success of the first print layer. The quality of this first layer is essential to obtain a complete quality part.
Incorrect calibration of the build plate can result in :
- If the nozzle is too far away from the printing plate, the extruded material will not adhere properly to the printing plate and the workpiece may not build up properly ;
- On the other hand, a material outlet nozzle that is too close to the build plate may prevent the material from extruding.
HoneyPrint software, the Pam controlling solution gives access to all these parameters and the user can modify them on its onw.
CAD - Computer Aided Design
Computer Aided Design, refers to all 3D creation techniques and software, such as Blender / 3D Slash / Clara.iow / selfcad.com / SketchUp / Blender / DesignSpark / LibreCAD / LibreCAD / Meshmixer / nanoCAD / FreeCAD / Sculptris / 3ds Max / nanoCAD / Onshape / Rhino3D / ZBrush / AutoCAD / CATIA / Fusion 360 / Siemens NX, etc.
Pollen AM has developed a technology that is agnostic towards CAD modelling solutions. It is compatible with the widest range of these software programs as long as they allow the export of 3D files in STL, AMF, 3MF, etc. file format.
s
Cartesian (3D printer)
Most FDM printers are of the Cartesian type. Their movement system is based on the Cartesian coordinate system in mathematics, this technology uses three axes - X (abscissa axis) / Y (ordinate axis) / Z (depth axis) - to determine the positions of the moving elements.
Generally, the so-called Cartesian printers have:
- a printing plate movable on the Z axis, an extrusion head movable on the X and Y axes;
- an extrusion head movable on the X and Z axes, and a printing plate movable on the Y axis.
Pam printers are systems that use Delta type displacements.
Cartesian coordinate
A Cartesian coordinate system is used to determine the position of a point in an affine space with a Cartesian coordinate system.
3D printers of the Cartesian and delta type use a Cartesian coordinate system.
Chemical resistance
Chemical resistance depends on the period of exposure, the temperature, the quantity, the concentration and the type of the chemical substance. In the case of chemical degradation of the material, the chemical reaction results in cleavage of the molecular chains. This process is generally preceded by swelling. In the course of degradation, materials lose strength, and in extreme cases this can lead to the disintegration of the material.
Compression set
Compression set [%] is determined by a constant deformation test over a period of 24 hours at 70 °C or 72 hours at room temperature and is standardized in DIN ISO 815. To achieve the best resistance to compression set annealing of the finished parts is recommended.
Comparative Tracking Index
Comparative Tracking Index - Tracking results from the progressive formation of conductive paths on the surface of a solid insulating material. It is generated by the action of electrical loading and electrolytic impurities on the surface. The Comparative Tracking Index (CTI) determined in accordance with IEC 60112 is the maximum voltage at which a material will withstand 50 drops of a defined test solution without tracking.
Coordinate system
In mathematics, a system of coordinates allows each point of a space to correspond to N dimensions.
There are several types of coordinates such as Cartesian or polar coordinates.
Creep behaviour
A pure elastic deformation behaviour, whereby the elastic characteristic remains constant, does not occur with any material. Due to internal friction, there exist at any time both a viscoelastic and a viscous deformation portion, causing the dependence of the characteristic values on the stress duration and intensity.
These non-elastic portions are considerably influenced by temperature and time. This dependence should be a pre-consideration in the case of plastics operating at ambient temperature under long-term load.
Behaviour under long-term static stress can be characterized according to ISO 899 nome by means of creep tests, whereby a test specimen is subject to tensile stress using a load.
The constant deformation thus caused is measured as a function of time. If this test is conducted applying different loads, the data yield a so-called isochronous stress-strain diagram.
Cura - Slicer
Cura is an open source slicing software developed by Ultimaker. It allows preparing 3D models to be printed.
Its open-source slicing engine is the result of several years of development over several years and has benefited from a large number of external contributors allowing continuous improvement of the software.
Cura users can use the software in simplified mode using already validated print profiles or in expert mode to adapt the printing parameters to the specific needs of the part to be printed. Cura offers more than 400 parameters for granular adjustment.
Pollen AM uses the Cura slicer for which add-ons have been developed.
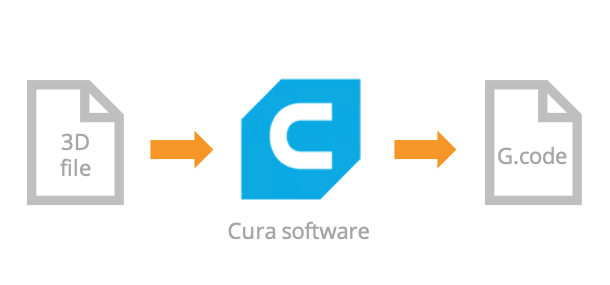
Curvilinear coordinate
Unlike the Cartesian coordinate system, the reference frame of a curvilinear coordinate system is not fixed, but depends on the position of a point in space.
Delta
There are more and more 3D printers of the Delta type. They work with so-called Cartesian coordinates. The printing plate is circular. The printing plate is circular.
Usually the so-called Delta printers have:
- A fixed printing plate, an extrusion head movable on the X (abscissa axis) / Y (ordinate axis) / Z (depth axis) axes, we then spoke of a "classic" delta printer.
- A print table movable on the X / Y / Z axes, a fice extrusion head, we then spoke of an "inverted" delta printer.
The movable part is fixed by three points and defines a triangular structure. Each of these attachment points moves on the Z axis, thus determining Cartesian coordinates.
The Pam printers developed by Pollen AM are Delta printers.
Dielectric constant
Dielectric constant is the ratio of capacity measured with the insulating material compared with that for air. This constant is determined in accordance with IEC 60250 and is temperature and frequency dependent.
Dielectric loss factor
When an insulating material is used as dielectric in a capacitor, an adjustment of the phase displacement between current and voltage occur. The displacement from the normal angle of 90 ° is known as the loss angle. The loss factor is defined as the tangent of the loss angle. As with dielectric constant, it varies with temperature and frequency. Values are provided for various frequencies at 23 °C.
Dielectric strength
Dielectric strength according to IEC 60243 is the ratio between disruptive voltage and the distance of the electrodes separated by the insulating material. Disruptive voltage is the a.c. voltage at which point the insulating material breaks down.
Electrical conductivity
The electrical conductivity of plastics is very low. They are, therefore, frequently used as insulating materials. Information on relevant properties for electrical applications must therefore be made available. Allowance should be made for the fact that resistivity and dielectric properties are dependent on moisture content, temperature, etc.
Elephant’s feet
The elephant's foot is a visible printing defect on the first layers of the part produced. To prevent the part from peeling off, many users tend to print very close to the manufacturing plate. This has the effect of distorting the first layers of printing which will be too wide.
To limit this, it's possible to reduce the temperature of the build plate, to increase the distance between the build plate and the material outlet nozzle, to reduce the horizontal expansion of the first layer, or to add a chamfer on the bottom of the part to be printed.
Endstop
The endstop , are mechanical, optical or magnetic components acting as a switch and allow defining a starting or arrival point.
The New Pam Series P and Pam Series M printers are composed of 15 endstop sensors to control the positioning of the build plate, to calibrate the flatness of the build plate, etc.
Extrude
Extrude means in the 3D world the action of creating a three-dimensional shape from a planar object. For example, by extruding a square over a height equal to its side, we obtain a cube. This term is also used in the world of 3D printing, in which it refers to the action of "making matter come out".
Extruder
In industry, an extruder is a machine used to extrude polymers. It comprises a material inlet called a hopper, a body formed by a cylinder in which a worm screw rotates and a head which serves as a support for a die.
Pollen AM has developed specific miniature extruders adapted to the constraints of 3D printing and allowing its users to free themselves from the limits linked to the use of filaments (diversity of materials, costs, etc.).
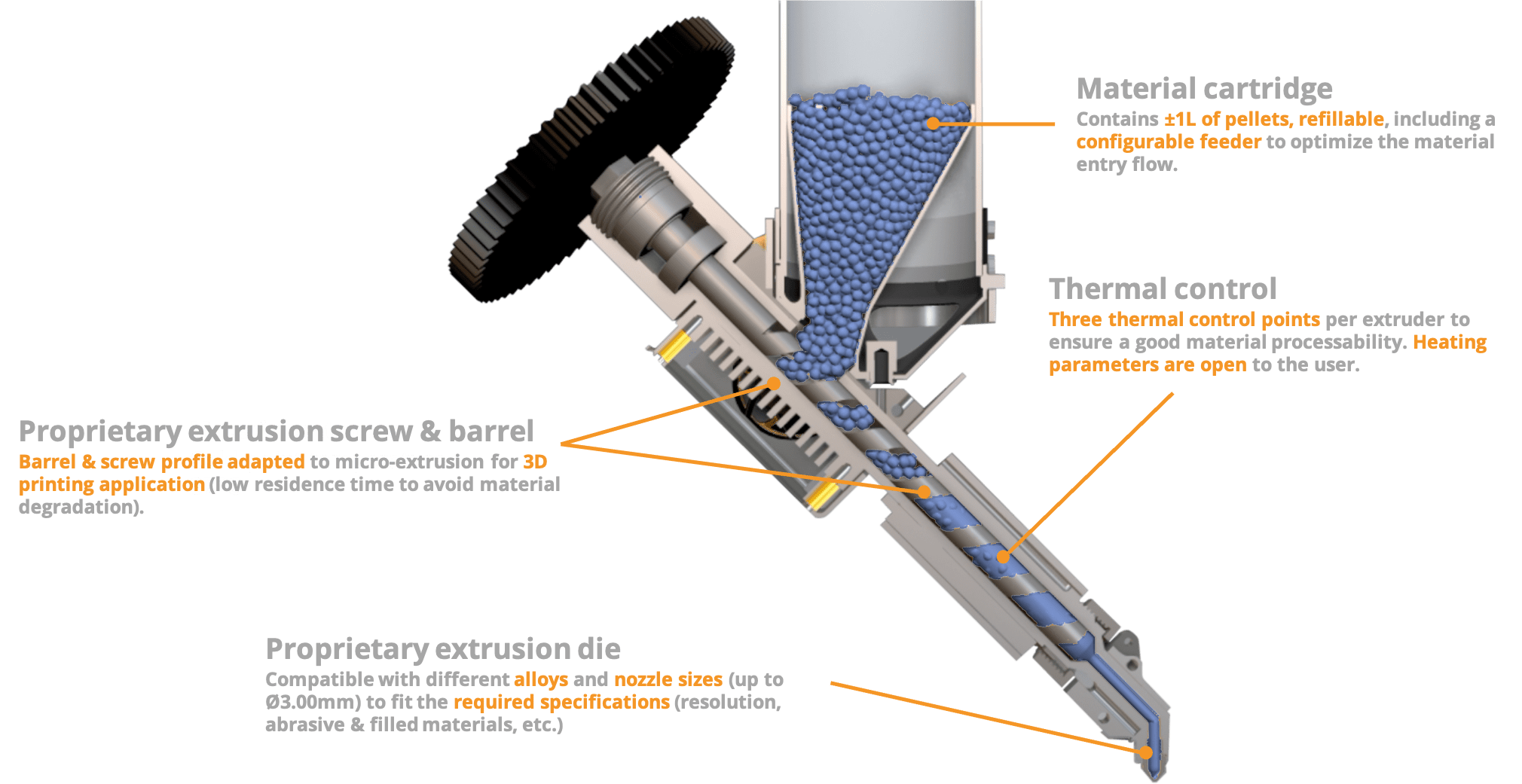
Extruder size
Also called material outlet nozzle size. The extruder size corresponds to the outlet diameter of the material nozzle, also called nozzle.
Pollen AM offers different material outlet nozzle diameters (Ø0.25; Ø0.40; Ø0.60; Ø0.80; Ø1.00 and Ø1.20 mm) as well as different alloys (brass, steel, other alloys are possible on request). Their geometry is specific and allows, among other things, a self-centring of the nozzles in relation to the extruder die.
FDM - Fused Deposition Modelling
FDM is a family of additive manufacturing technologies.
This family of technology is based on three main elements :
- a manufacturing tray on which the item is printed;
- a printing material that can take the form of a filament we will then speak of FFF technology or directly of pellets;
- an extruder.
Pam's technology is part of the FDM family.
Filament
The filament is the consumable of the FFF type printers. It is usually a coil of filament material that is progressively melted through the extruder in order to model layer by layer the part to be produced.
By directly using industrial pellets, the Pam technology frees itself from filaments and allows to free itself from its constraints (availability of materials, sourcing, costs, nature, etc.).
Fire behaviour
Like all organic materials, plastics are flammable. The primary and secondary fire properties for them are classified according to various norms and standards.
Primary fire properties:
- Flammability and active continued burning
- Contribution to flame spread
- Release of heat
Secondary fire properties:
- Flaming droplets / particles
- Smoke density
- Smoke toxicity
- Corrosiveness of fire gases
As the fire properties are very often tested on the end product, the design and the structure of the end product has a substantial impact on the subsequent fire properties.
For example:
- The thickness of a cable sheath is crucial for the smoke density that is to be expected.
- The respective fire scenario has a crucial bearing on the application of a particular test.
- If the components are subsequently to be fitted in rail vehicles, for example, tests in accordance with DIN EN 45545 are relevant.
- In automotive construction, the tests conducted include those according to FMVSS 302.
The fire properties of the individual materials can be very different in the different fire scenarios. The results cannot simply be transferred from one test to another, which makes it more difficult to make predictions when choosing materials for new applications.
For instance, materials displaying very good cable fire properties do not necessarily receive a good classification according to UL94V.
One of the ways to improve the quality of such predictions is to use the cone calorimeter, which can be used to determine many material-specific properties.
Firmware
The firmware is an integrated machine firmware, this software is present in an electronic board and make the interaction between several components.
The printers developed by Pollen AM integrate 11 electronic cards and the same amount of firmware. These firmwares integrate, for example, mathematical models to manage travel.
Food contact
To determine the material suitability for certain food applications a thorough evaluation by the processor(s), manufacturer(s) and/or distributor(s) is required. Where specific regional regulations do not exist, the current legal EU and US requirements as well as globally accepted standards for consumer articles, food contact articles and medical devices should be used as reference.
G-Code
G-code is a machine language developed by the EIA (Electronic Industries Alliance) in the early 1960s and then standardized by ISO in 1980 under the reference RS274D/ (ISO 6983). The G-code file is used to define sequences of instructions to control numerically controlled machine tools.
Originally developed for cutting machine tools, the G-code is used in a very wide range of manufacturing applications with adaptations :
.
- machining by material removal: turning, milling, drilling, engraving, routing ;
- cutting with: knife, laser, water jet, plasma, flame or oxidation ;
- punching ;
- additive manufacturing.
The printers developed by Pollen AM execute a G-Code file to produce a part. This file is obtained after the slicer interprets a 3D model.
Feeder
The feeder is a component in the feed hopper (also called a material cartridge) of the Pam systems, its purpose is to avoid bridge structures that could be created at the extruder inlet, thus maximizing a constant throughput.
Gas permeability
The passage of gas through a test specimen is called diffusion.
This takes place in three stages:
1. Solution of the gas in the test specimen ;
2. Diffusion of the dissolved gas through the test specimen. ;
3. Evaporation of the gas from the test specimen.
The diffusion coefficient Q [m2 / (s · Pa)] is a material constant which specifies the volume of gas which will pass through a fixed time, with a given partial pressure difference.
The coefficient varies with temperature and is determined in accordance with DIN 53536.
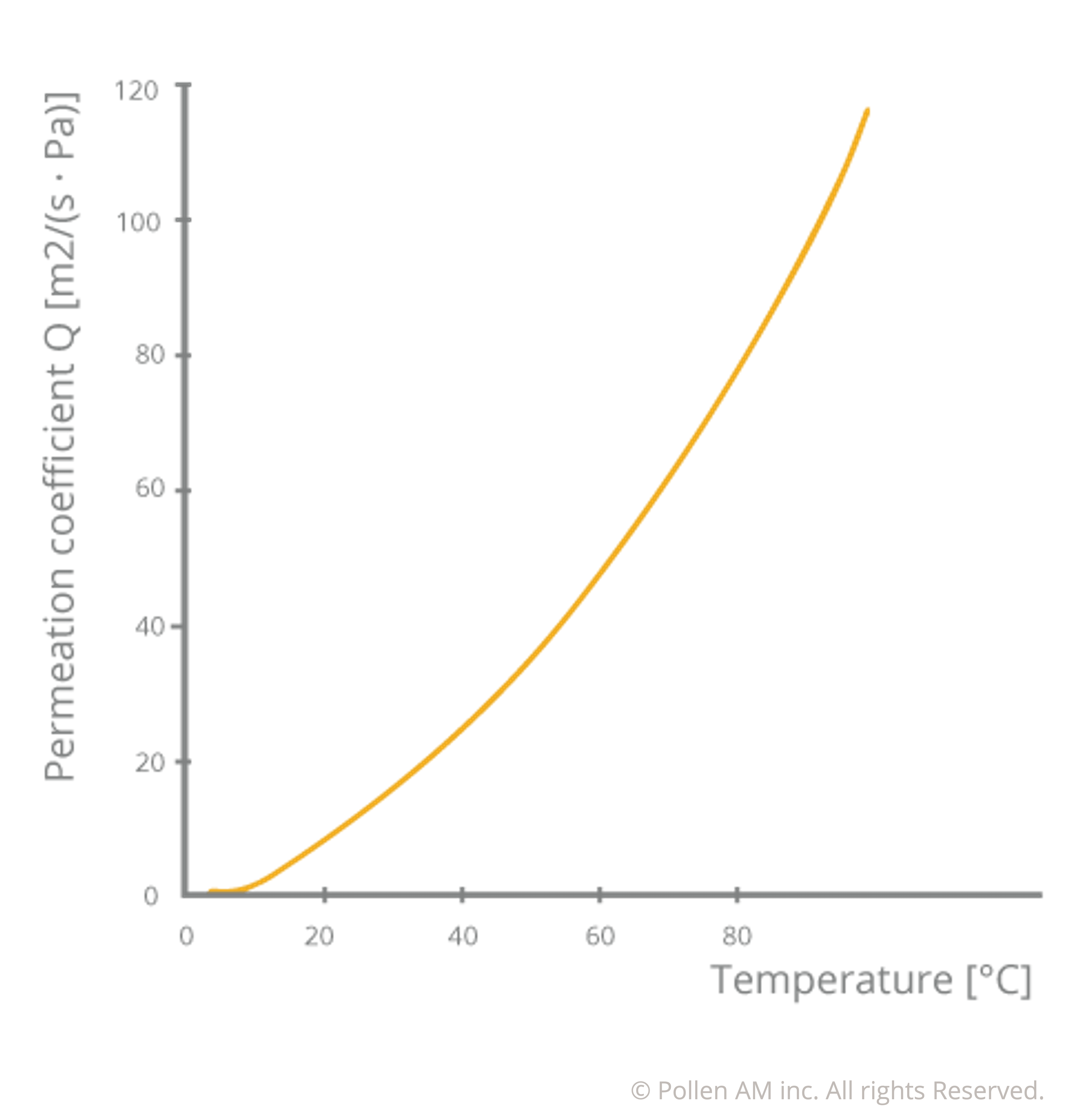
Glass transition
The glass transition temperature (Tg) of a plastic is the point at which a reversible transition of the amorphous phases from a hard and relatively brittle condition to a viscoelastic or elastomeric condition occurs. The glass transition takes place over a more or less wide temperature range and varies according to the hardness of the material and its amorphous character. The larger the amorphous part, the lower the glass transition temperature and the narrower the temperature range.
There are several methods for determining the glass transition temperature, each of which may give a different value, depending on the test conditions. Dynamic tests give higher temperature values than static tests. The thermal history of the material to be measured is also important. Therefore, similar methods and conditions should be selected to compare the glass transition temperatures of different products.
Heat deflection temperature
Similarly to the Vicat test, the test set-up is heated in a heat transfer medium at a rate of 120 K/h. The arrangement is designed as 3-point bending test, the test piece being stressed at a constant load which corresponds to a bending stress of 1.80 MPa, 0.45 MPa or 8 MPa (method A, B or C), depending on the rigidity of the material. The temperature at which the test piece bends by 0.2 to 0.3 mm (depending on the height of the test piece) is indicated as HDT.
Heatbed
The heatbed refers to the heated build plate.
Heated room
Controlling the thermal properties of polymers throughout their transformation cycle is essential (from their melting in the extruder to their deposition on the manufacturing platform). This is particularly true for semi-crystalline and performance materials.
For example, if the temperature of the workpiece during manufacture is not sufficient, this will result in layer delamination, deformation, dimensional variations, poor crystallization, etc. The use of a heated manufacturing build plate, a closed manufacturing unit is not sufficient to transform performance materials. Therefore, it is necessary to use a heating build chamber to guarantee a constant and homogeneous temperature in the manufacturing unit throughout its volume.
The heating chambers developed by Pollen AM are equipped with two sub-assemblies :
- global equipment : air recirculation and forced air heating solution allowing maintaining the manufacturing unit at temperature (up to 70°C).
- a local equipment : heating system called radiant plate ( up to 300°C) allowing maintaining the last printed layers of the object during the manufacturing process at temperature, improves the interlayer adhesion, allows a better management of the recrystallization of materials (semi-crystalline), limits the "bananage" effect, etc.
.
The manufacturing chamber (heated up to 70°C maximum) is an accessory that mainly provides a thermally stable and homogeneous environment. The radiant plate is the key equipment for local thermal management of the materials being manufactured, reducing shrinkage stresses and deformations during the crystallization phase.
Heating cartridges
Heating cartridges are cylindrical electrical resistors. Protected by a steel shield, the thermal flux or specific power, can reach up to 50 W/cm2 and the operating temperature up to 800°C.
Generally used for heating solids such as press platens and tools, they can also be used for heating water or gas under certain conditions. Widely used in the plastics and rubber industry for automotive, food and 3D printing, they are a key element in the thermal management of Pam systems.
High energy radiation
Resistance to α-, β- and γ-radiation is dependent on such factors as the intensity of the radiation, the shape and dimensions of the test specimen, and the atmosphere in the test area. The addition of crosslinking agents and subsequent β- and γ-radiation can affect crosslinking of thermoplastics. This is a method to improve short-term heat deflection temperature and chemical resistance.
HIPS - Material
HIPS is an impact modified polystyrene resins and has a good impact strength and chemical resistance. Commonly used as a support material in 3D printing compatible with ABS and other styrenic based polymers. HIPS is used in a large variety of applications such as food packaging, home appliances, toys, sport & leisure, hygiene & personal care, etc.
Hollow
Hollow refers to a part with an Infill of 0%. This means that the printed part has only walls and an empty interior.
HPP - Material
High Performance Polyester offers strength and durability that provides an outstanding combination of mechanical properties and toughness. Chemical resistance and hydrolytic stability are improved compares to other copolyesters. Reinforced with glass are good candidates for (mechanical and electrical uses at elevated temperatures. HPP is neutral in taste, food, heat resistant, unbreakable, it is a good alternative to the PC. It is often used for the production of housewares, appliances, electronics and healthcare.
Infill
Infill is an important parameter that represents the fill rate of the part to be produced. This parameter is expressed as a percentage. An infill of 0% will allow the production of an empty part (Hollow), an infill of 20% means that the inside of the part will be composed of 20% material and 80% vacuum. An infill of 100% means that the part will be completely full.
In addition to the infill percentage, it is also possible to vary the infill geometries. Cura offers 13 different impacting infill geometries, production times and mechanical properties of the parts.
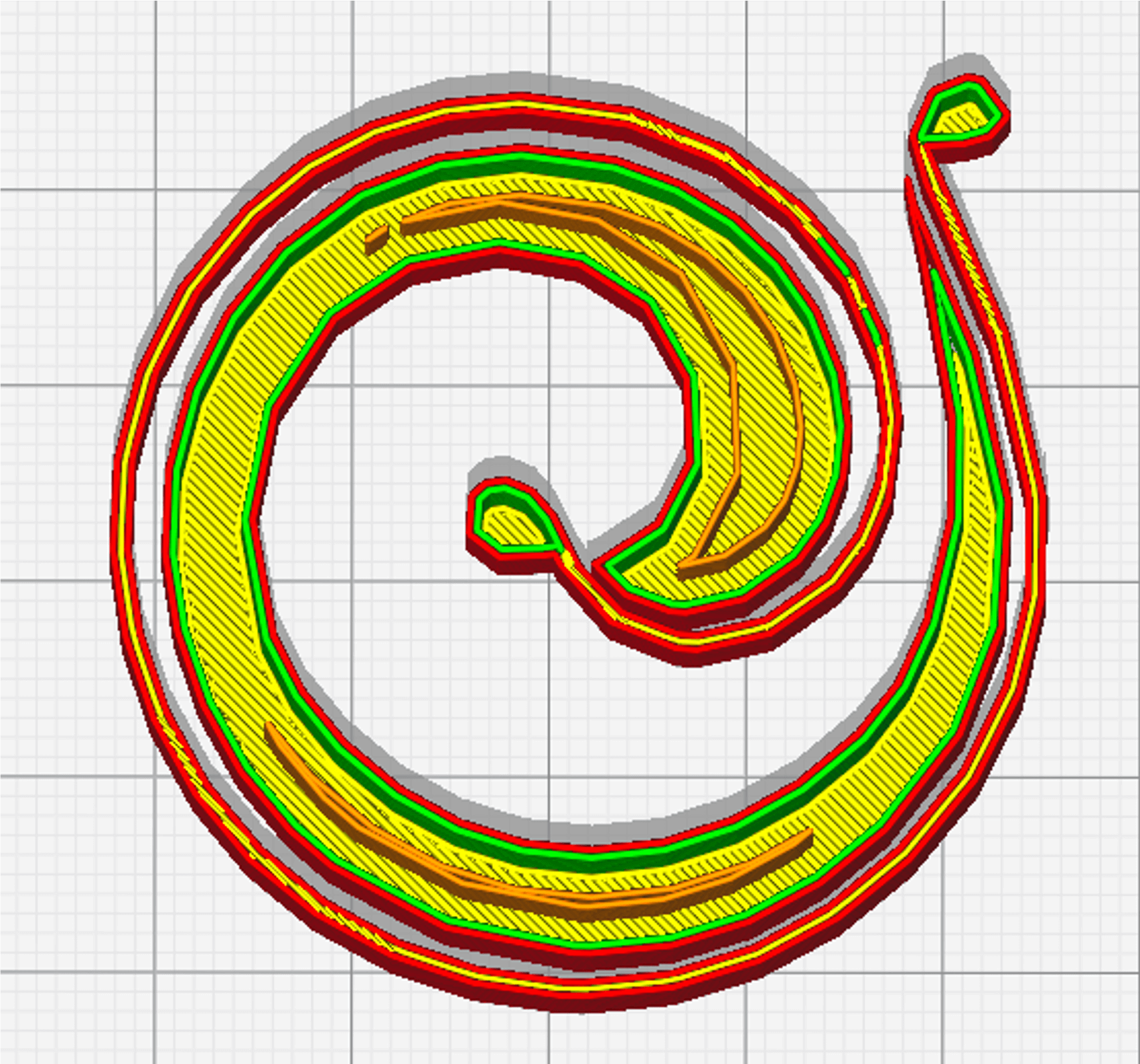
The concentric infill pattern is a 2D model consisting of producing concentric circles in the image of walls. The spacing between the concentric circles is a function of the chosen infill rate. The higher the infill rate, the smaller the space between the circles; conversely, the lower the infill rate, the larger the spacing between the circles.
When printing so-called semi-flexible parts, it can be useful to use infill patterns that preserve the flexible nature of the material. Infill patterns such as Concentric, Cross and Cross 3D are so-called "flexible" printing patterns.
Recommended infill percentages : 20 to 100 %.
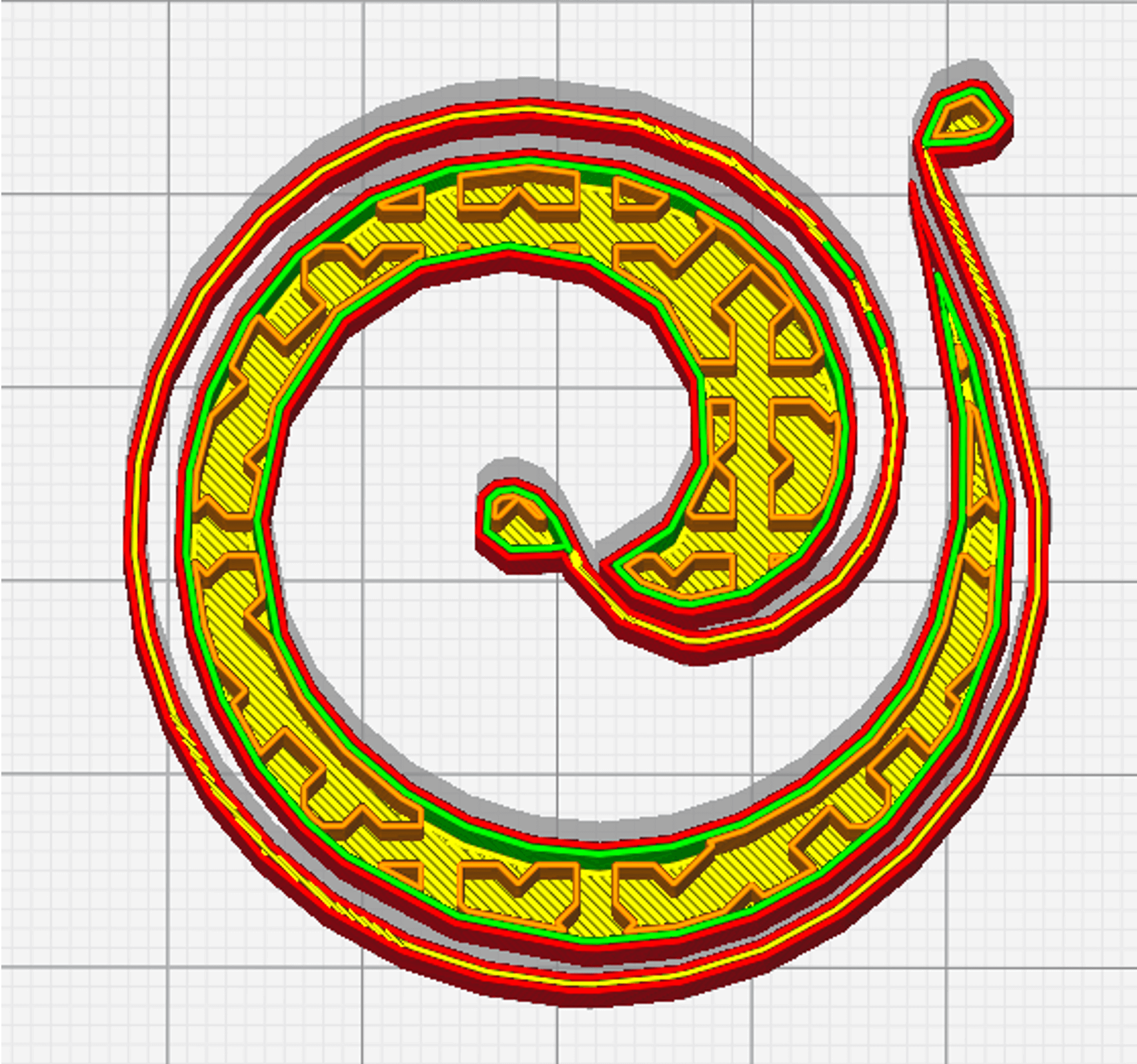
The Cross infill pattern is a 2D model producing "cross" shaped grids. The spaces between the crosses and the grids allow to obtain a more or less large flexibility.
When printing so-called semi-flexible parts, it can be useful to use infill patterns that preserve the flexible nature of the material. Fill patterns such as Concentric, Cross and Cross 3D are so-called "flexible" printing patterns.
Recommended infill percentages : 20 à 100 %.
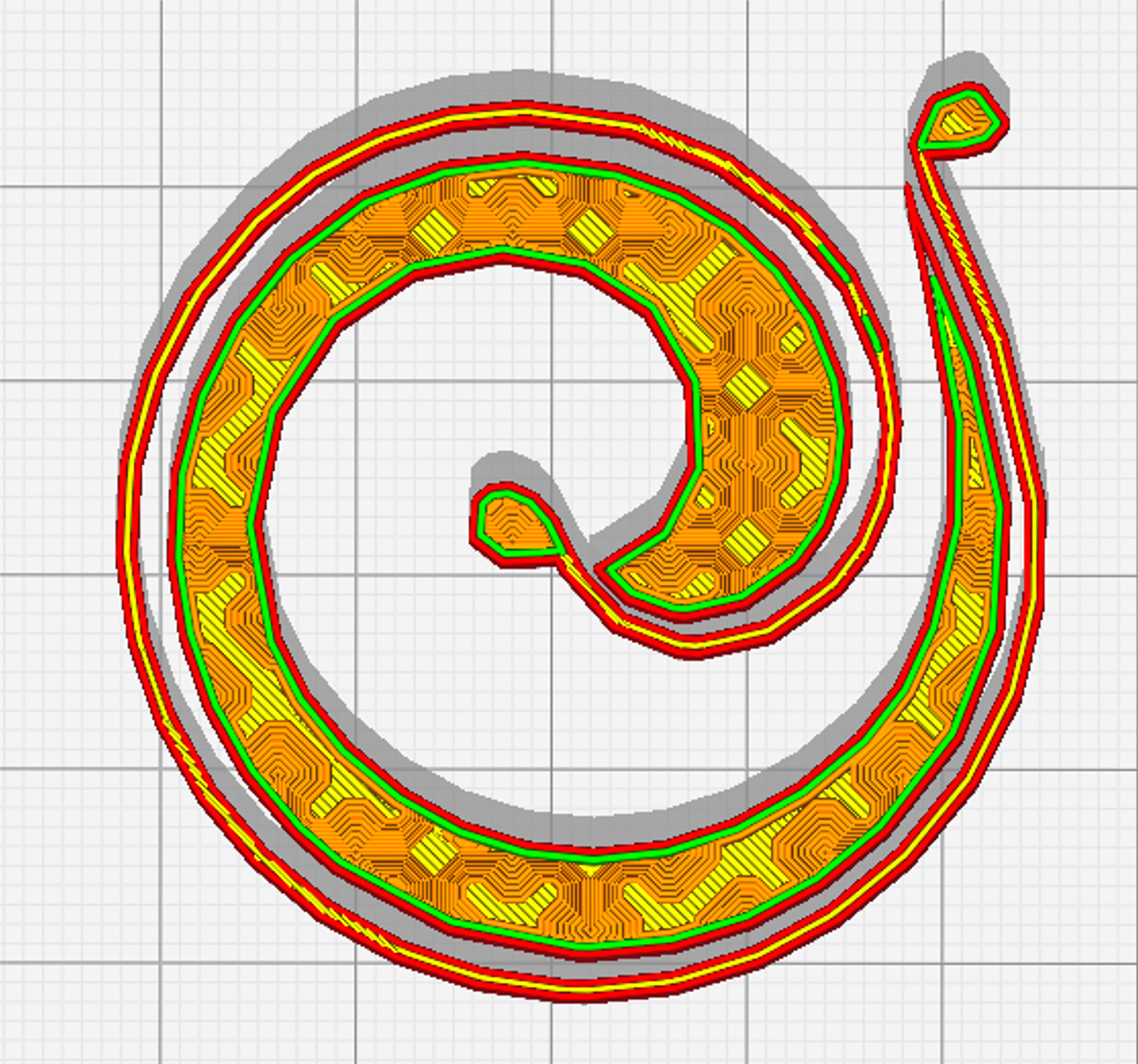
The Cross 3D infill pattern is similar to the Cross fill pattern. However, the grids produced in the shape of a "cross" are sometimes tilted (in Z).
A part produced with a Cross 3D infill patterns will have a higher stiffness than the same part produced with a Cross infill pattern for the same fill rate.
When printing so-called semi-flexible parts, it can be useful to use infill patterns that preserve the flexible nature of the material. Infill patterns such as Concentric, Cross and Cross 3D are so-called "flexible" printing patterns.
Recommended infill percentages : 20 à 100 %.
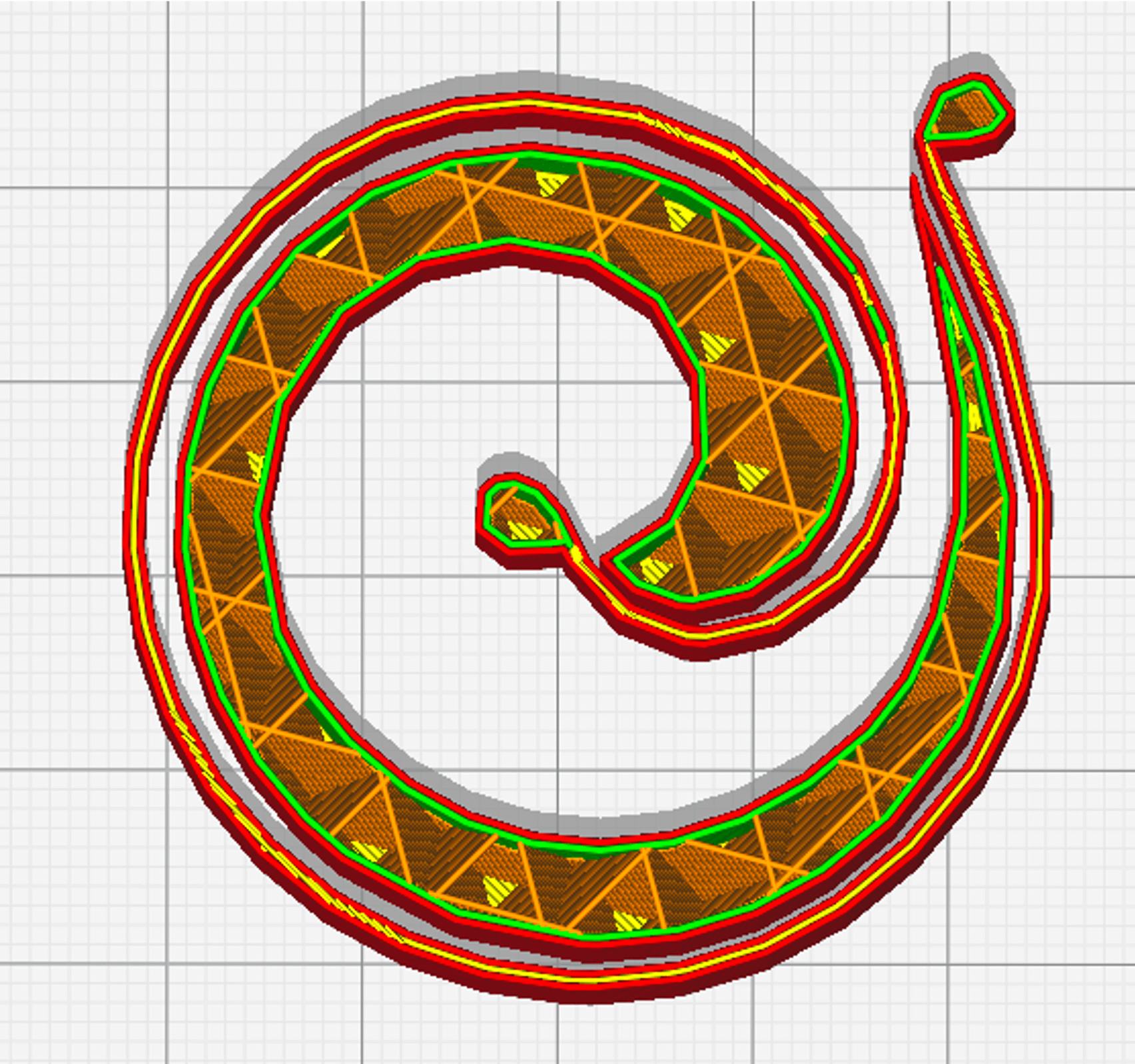
The Cubic fill pattern is a 3D infill pattern of inclined cubes.
This infill pattern is recommended for the production of rigid and functional parts that need to withstand multiaxial stresses; such as a shelf bracket, for example.
Recommended infill percentages : ±s 50 %.
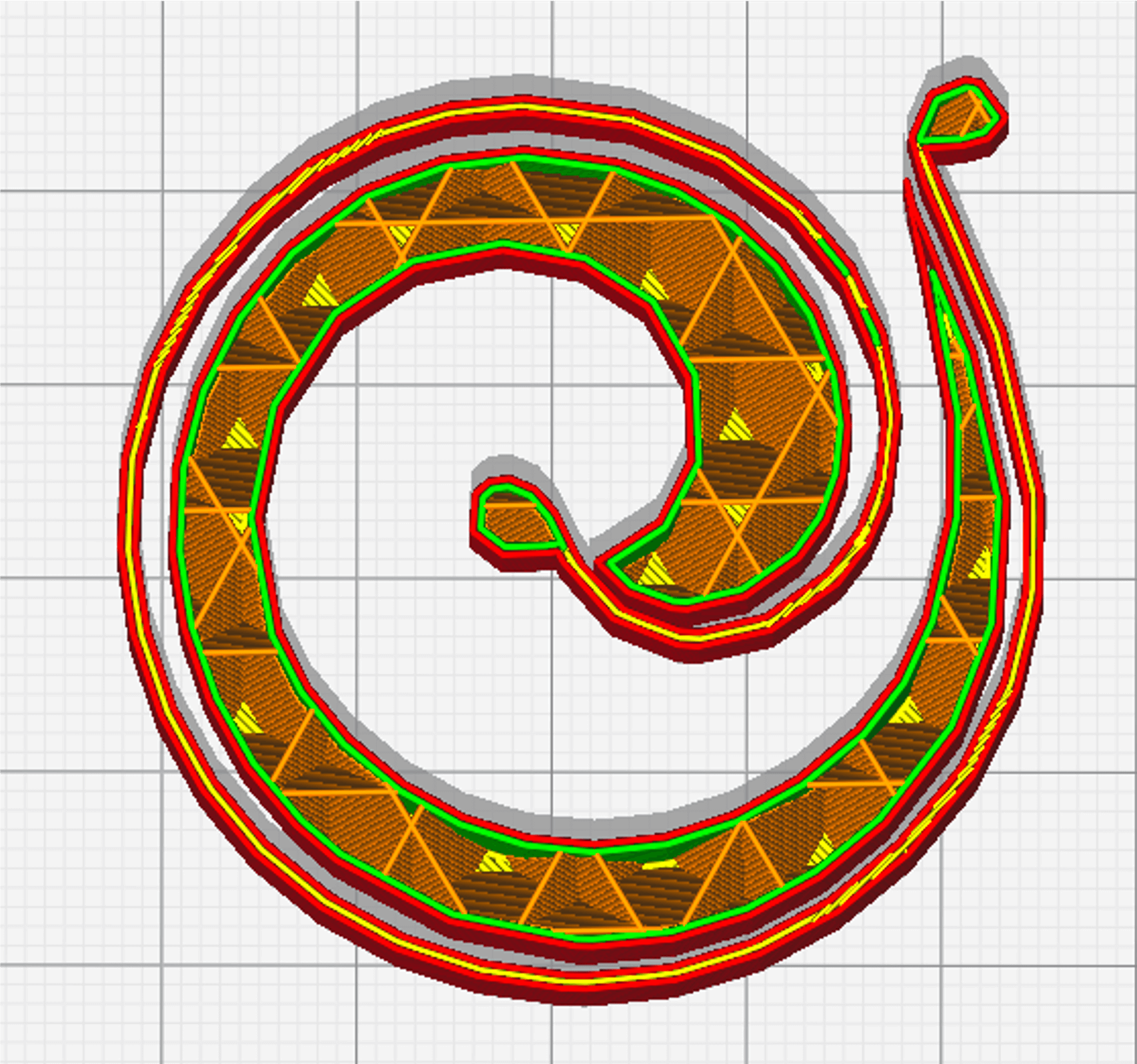
The Cubic subdivision fill pattern is a 3D infill pattern similar to the Cubic pattern (assembly of inclined cubes). It has the advantage of using less material than the Cubic fill pattern for the same percentage fill.
This infill pattern is recommended for the production of rigid and functional parts that need to withstand multiaxial stresses; such as a shelf bracket, for example.
Recommended infill percentages : ± 50 %.
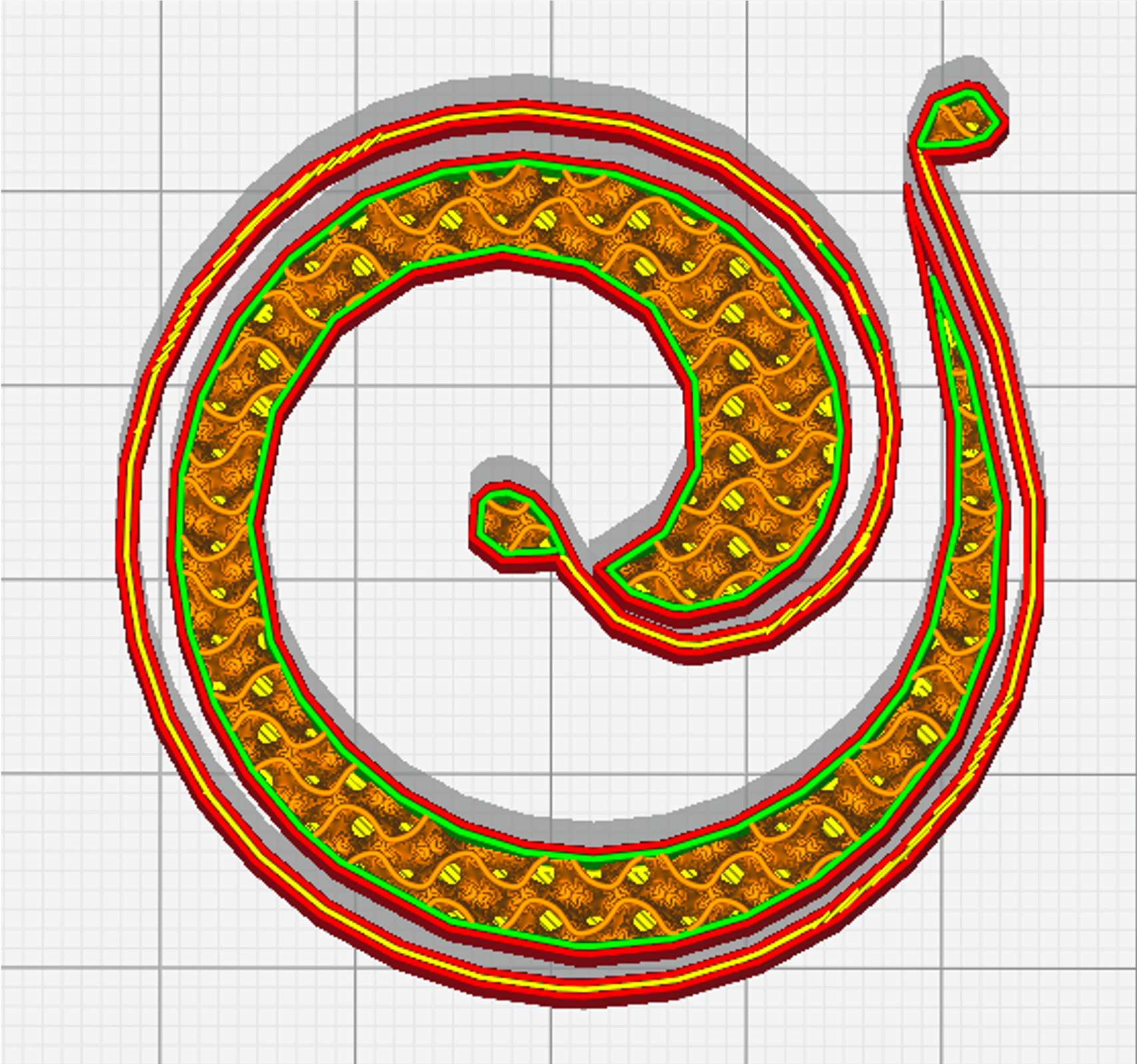
The Gyroid infill pattern is a particularly unique 3D pattern, it describes a three-dimensional sinusoidal periodic progressive waveform".
This infill pattern is recommended for the production of rigid and functional parts that need to withstand multiaxial stresses; such as a shelf bracket, for example.
Recommended infill percentages : ± 50 %.
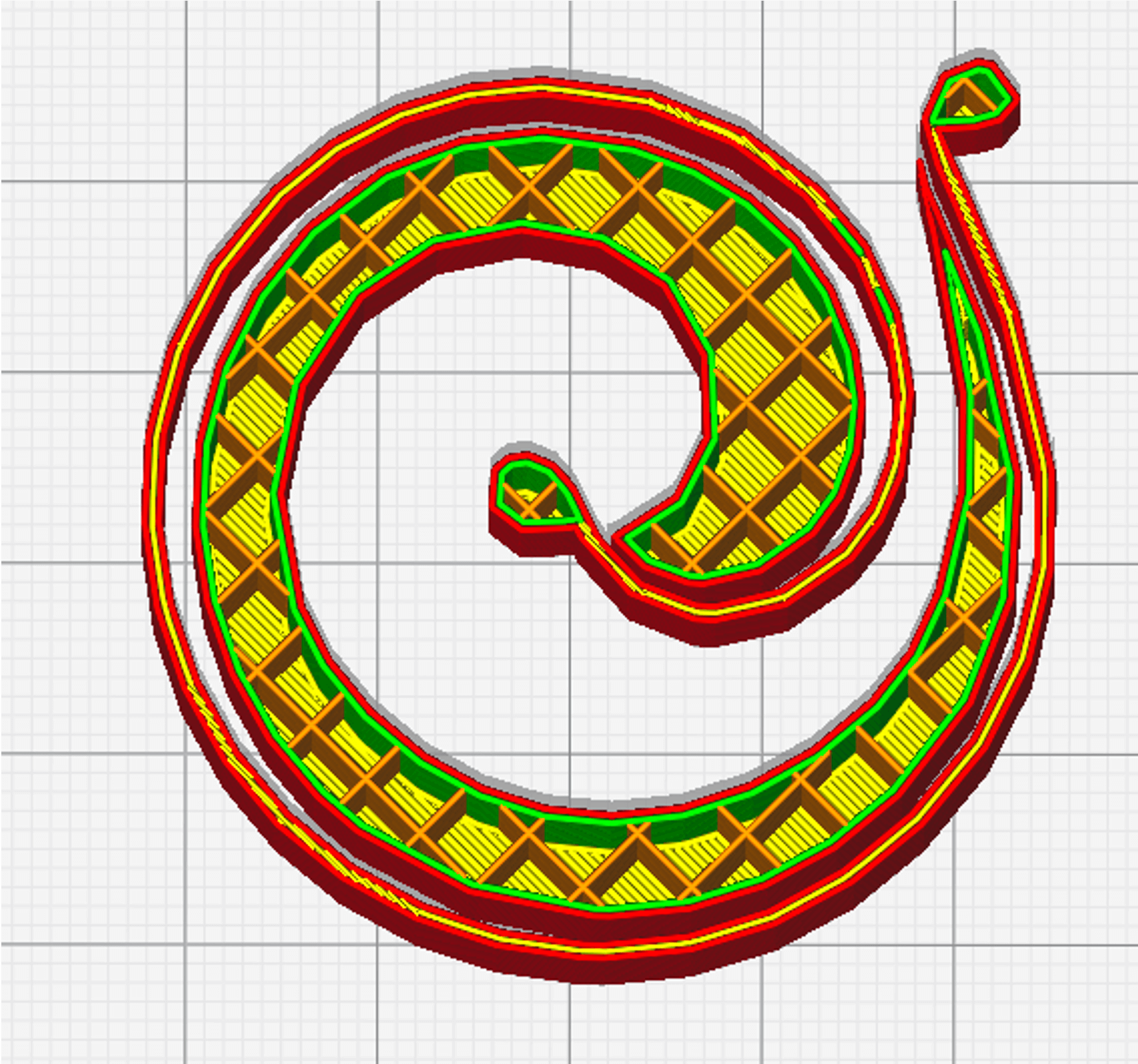
The Grid infill pattern is an explicit 2D pattern. It describes the production of a grid on a single plane.
This pattern can be recommended for the production of parts with low mechanical stress, as can the Triangles and Tri-hexagon infill patterns, which can increase the printing time by up to 25% compared to the Grid.
Recommended infill percentages : ± 50 %.
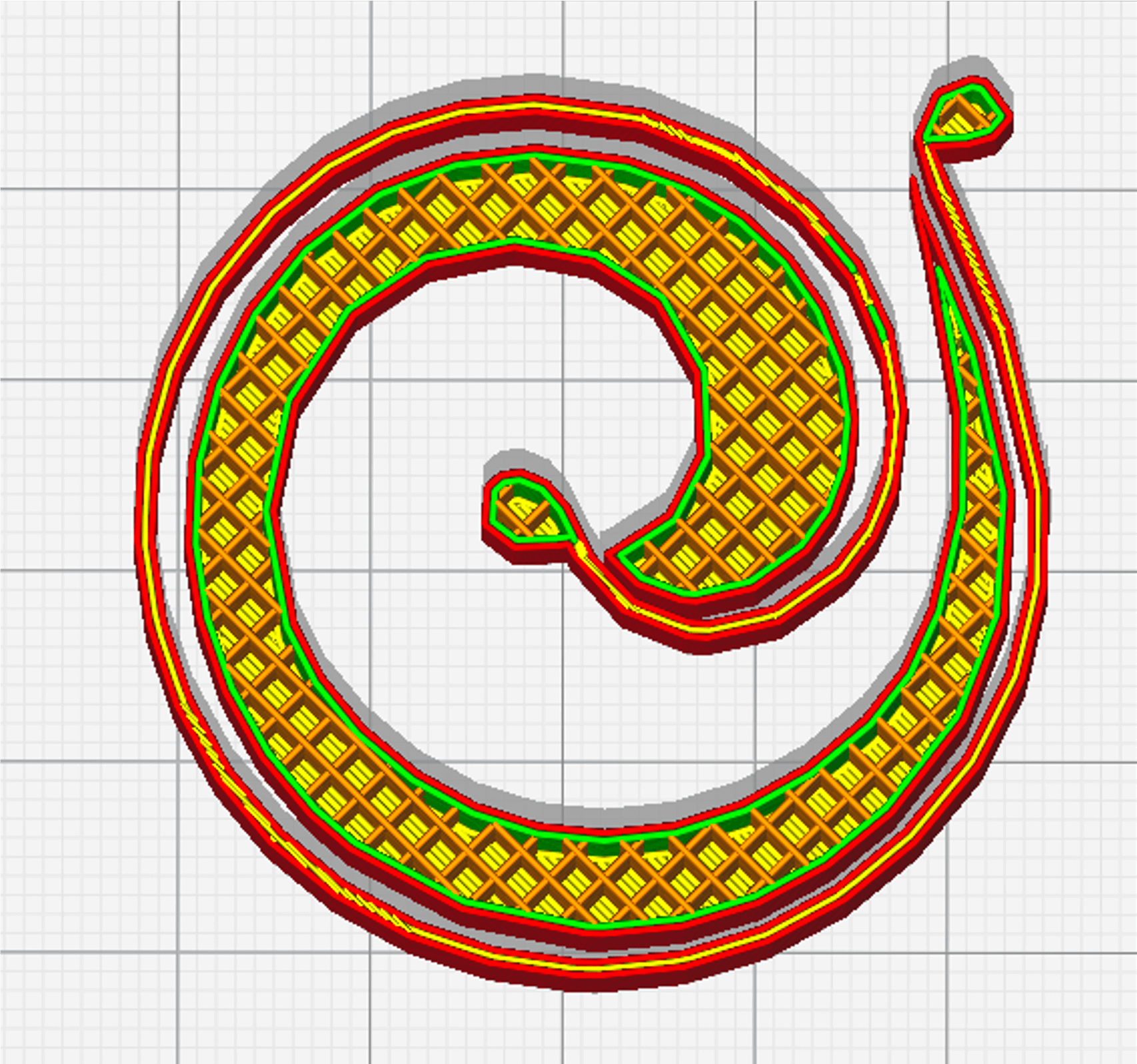
The Lines infill pattern is a 2D pattern. It describes the production of lines sequentially on the same plane, so the printer will "retract" from one infill line to another. It is possible to vary the infill angle from one layer to another from 0 to 180° with no layer limit. This makes it possible, for example, to create internal structures with specific mechanical properties, impossible with conventional production methods (rebound, mechanical resistance, etc.).
This infill pattern is similar to the Zig-Zag pattern.
This pattern can be recommended for the production of "fast" parts.
Recommended infill percentages : 20 to 100 %.
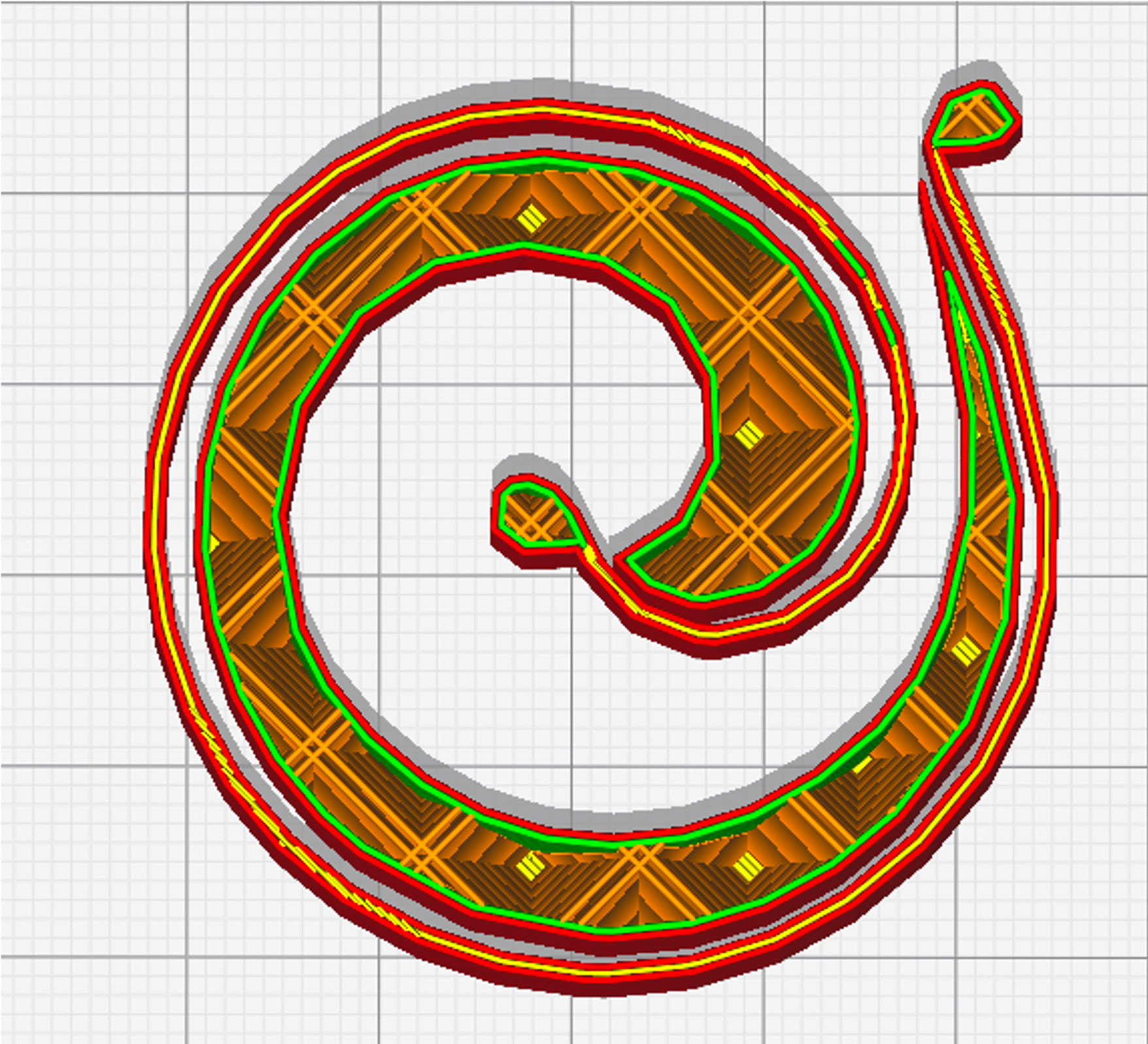
The Octet infill pattern, also called tetrahedral, is a 3D fill pattern assembling pyramids with a rectangular base.
This infill pattern is recommended for the production of rigid and functional parts that need to withstand multiaxial stresses; such as a shelf bracket, for example.
Recommended infill percentages : ± 50 %.
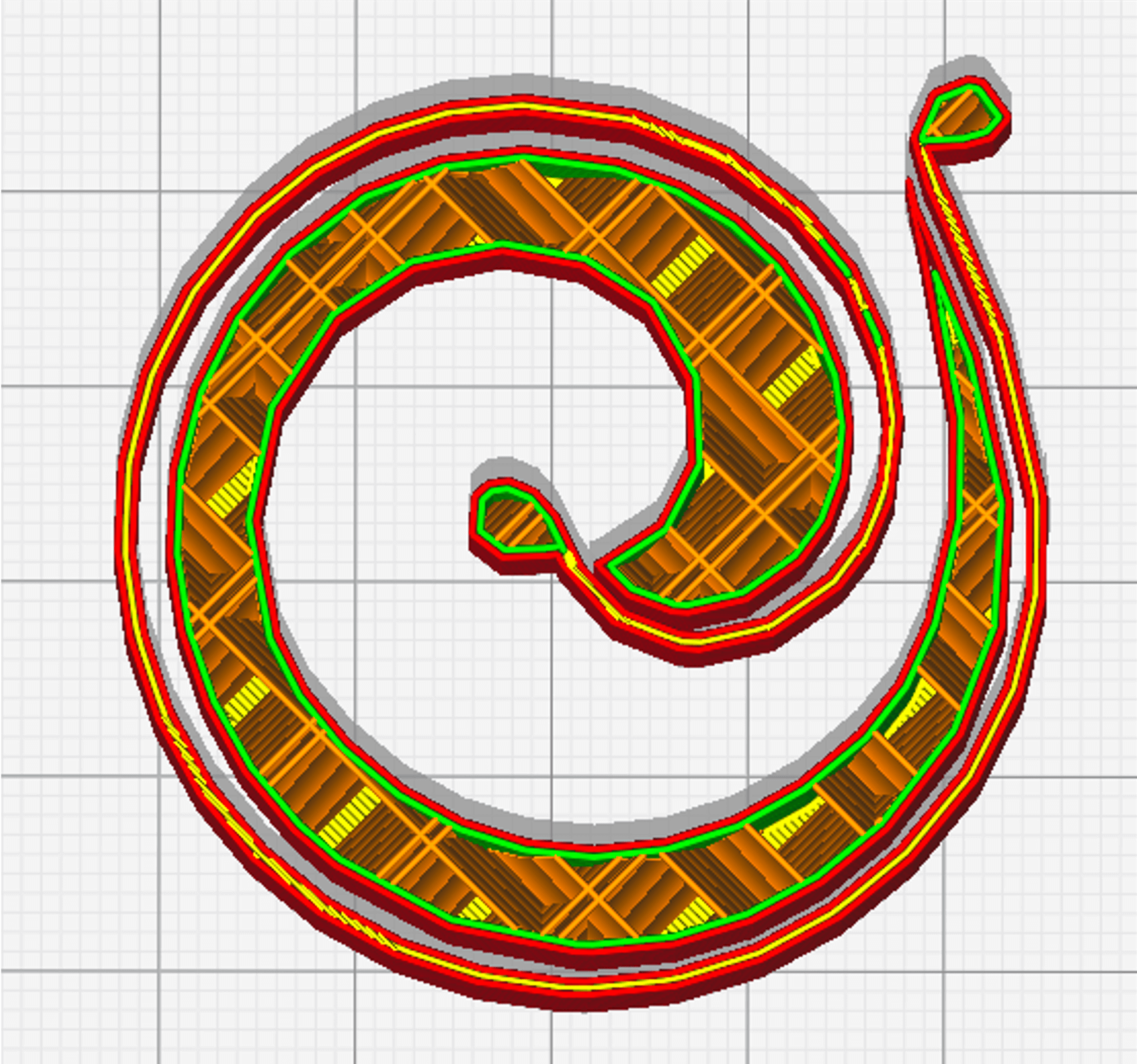
The Quarter Cubic infill pattern, is a 3D infill pattern assembling pyramids with a rectangular base, 50% of which are offset from each other. The printed part has a complex internal structure.
This infill pattern is recommended for the production of rigid and functional parts that need to withstand multiaxial stresses; such as a shelf bracket.
Recommended ininfill percentages : ± 50 %.
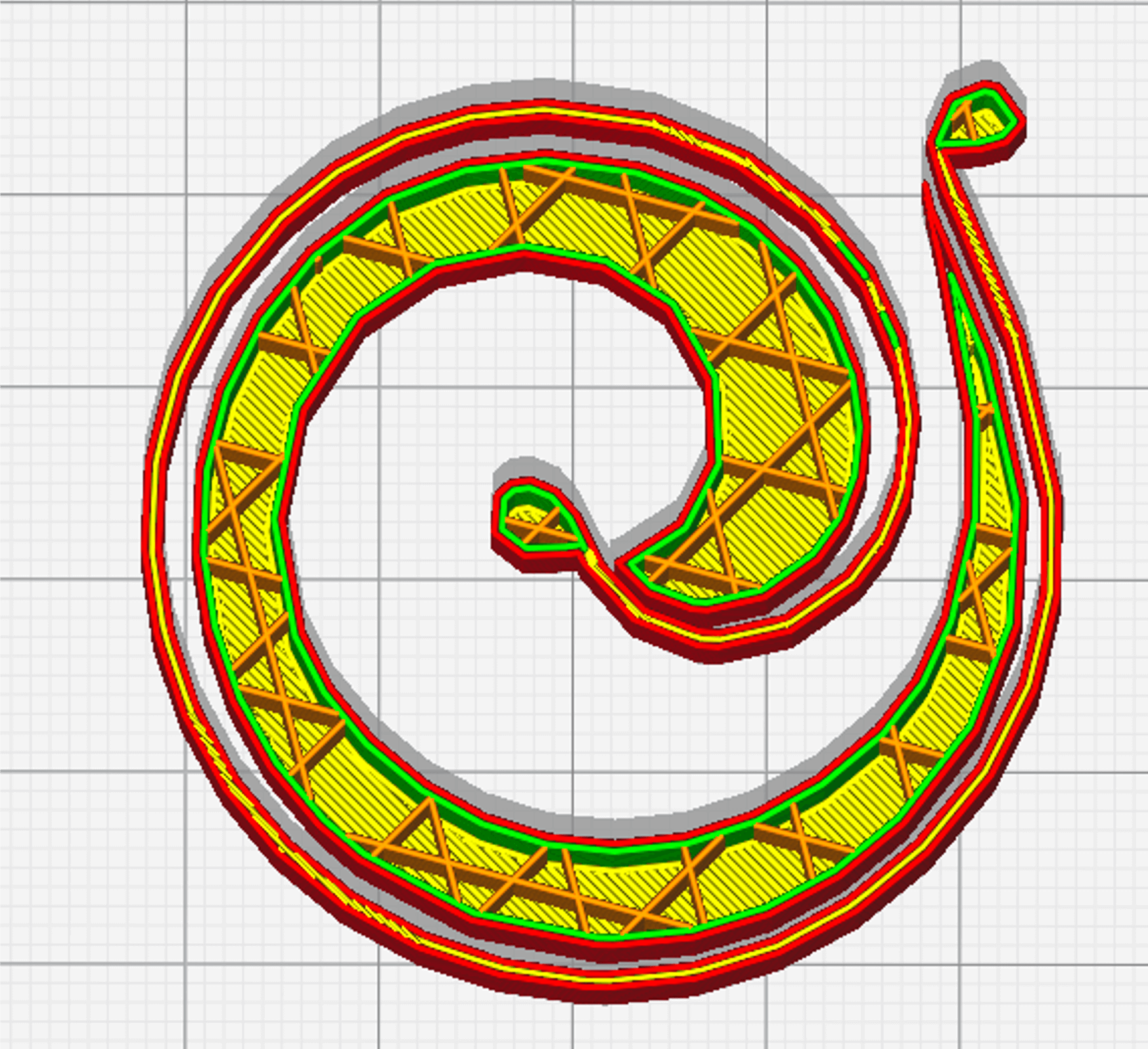
The Tri-Hexagon infill pattern is a 2D pattern dedicated to prototyping. Like the Grid and Triangle patterns, it is mainly used for the production of prototypes and / or parts with low mechanical stress.
This infill pattern describes the production of hexagons intersected by triangles. The hexagon being an efficient geometry, from a mechanical and material consumption point of view, it seems to allow the production of stronger parts than those integrating a Grid or Triangles infill pattern and this for the same percentage of infill.
This pattern can be recommended for the production of parts subject to low mechanical stress, as can the Triangles and Grid infill patterns.
Recommended infill percentages : > to 50 %.
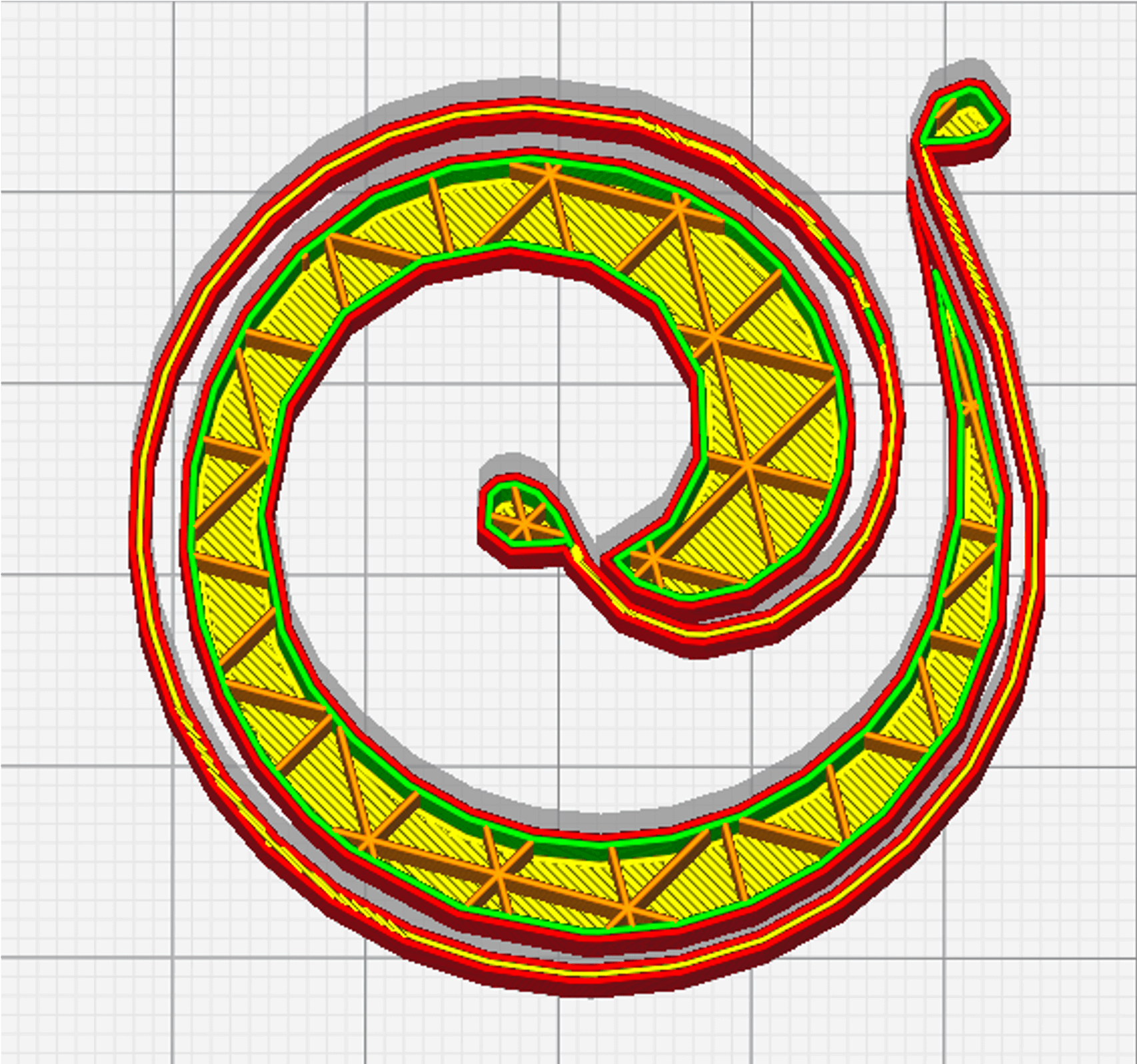
The Triangles infill pattern is a 2D mesh consisting of triangles. This infill pattern has an advantage in terms of mechanical strength when a stress is applied perpendicularly to one side of the printed part. Like the Grid and Tri-Hexagon patterns, it is mainly used for the production of prototypes and/or parts with low mechanical stress.
Recommended infill percentages : > to 50 %.
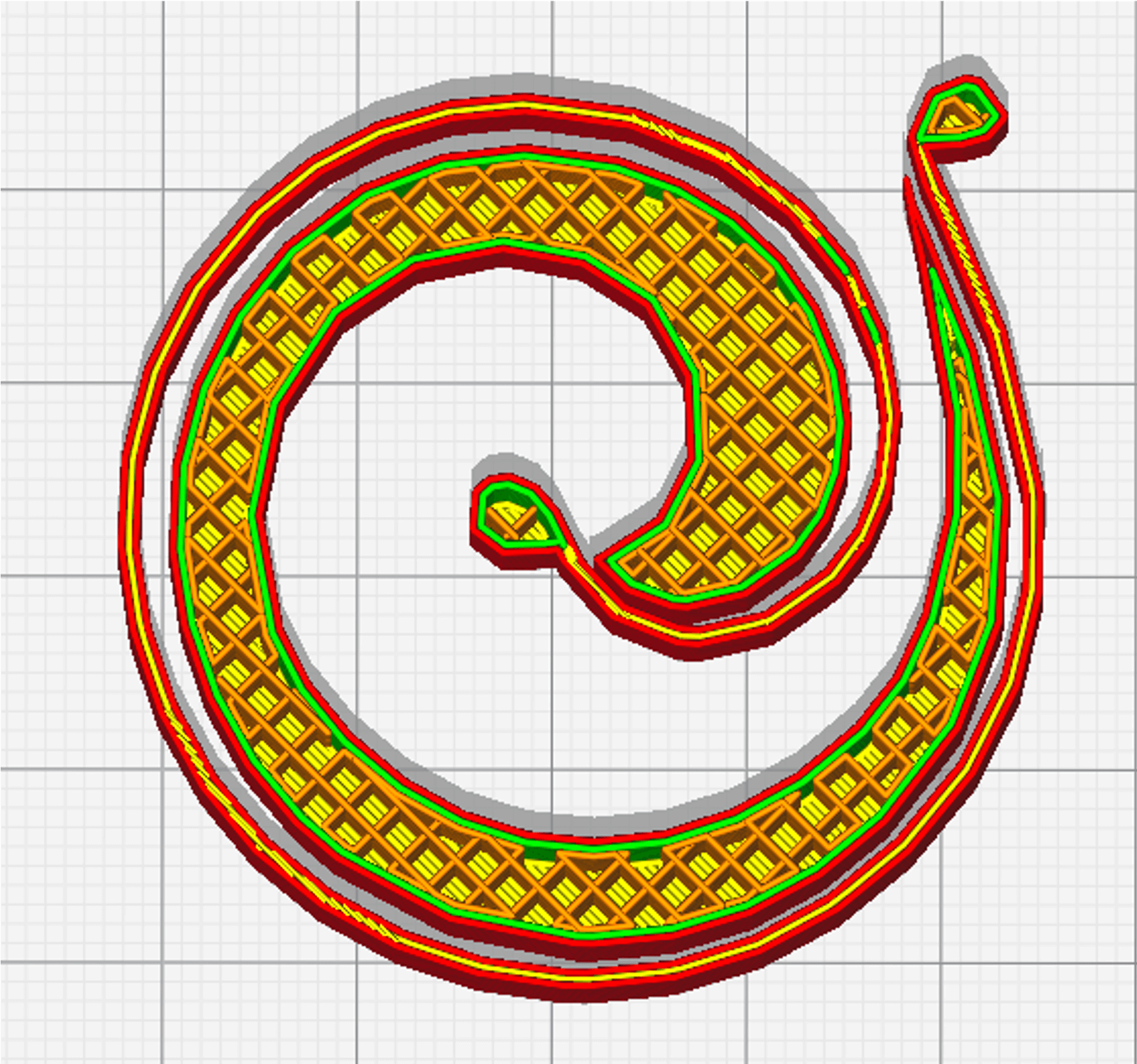
The Zig-Zag infill pattern is a 2D pattern. It describes the production of continuous lines on the same plane. It is possible to vary the infill angle from layer to layer from 0 to 180° without layer limitation. This makes it possible, for example, to create internal structures with specific mechanical properties that are impossible with conventional production methods (bounce, mechanical strength, etc.).
This infill pattern is similar to the Lines pattern.
This pattern can be recommended for the production of "fast" parts.
Recommended infill percentages : 20 to 100 %.
Islands
The islands are small contact points of a part of the manufacturing platform. They have a small contact surface with the production table and are susceptible to peeling off during the production cycle. To limit this effect, it may be necessary to print a Brim.
Layer height
The layer height defines the height of the deposited layers of material. This parameter is important and influences both the fineness of the part and the production times.
The thinner the layer height, the smoother the final part will look, and the longer the production time will be. Conversely, the higher the layer height, the more strategic the final part will look and the shorter the production time.
Limonene
Limonene exists in two isomeric forms (d- and l- limonene).
D-limonene is a natural constituent of certain trees, plants, fruits and vegetables. It is found, among other things, in the peel of citrus fruits (orange, lemon, lime, etc.).
The other isomer (l-limonene) is mainly found in pine oils, turpentine and mint oils.
D-limonene is used as:
- metal degreasing agent ;
- flavouring agent in food, non-alcoholic beverages ;
- aroma in soaps, perfumes and cleaning products ;
- wetting and dispersing agent ;
- solvent;
- cleaning agent / degreaser, etc.
D-limonene is used in 3D printing as a solvent for some thermoplastics such as HIPS for example.
Contact with this molecule can cause allergic reactions and respiratory genes in some individuals, therefore Pollen AM recommends that users refer to the product data sheet and HSE services before using this product.
Material cartridge - Hopper
Elements for feeding the extruder with raw material (thermoplastic pellets).
The material cartridges developed by Pollen AM have a capacity of ±1L, are refillable on the fly, even during a production cycle.
Each material cartridge is equipped with a feeder to limit bridge structures that can occur in the material feed.
The new material cartridges are equipped with an internal geometry that optimizes the flow of the pellets into the extruder.
Material cartridges can be developed to measure. Do not hesitate to contact the Pollen AM teams to discuss your project.
Maximum service temperature
The life expectancy of a finished TPU part will be influenced by several factors and is difficult to predict exactly. In order to be able to compare materials with one another under the aspect of “maximum service temperature”, prolonged storage tests according to DIN EN ISO 2578 at various temperatures are used to ascertain so-called “long-term air ageing”
Mechanical testing
The purpose of studying the mechanical behaviour of materials is to find out how they respond to a given load. There are several large families of mechanical tests such as hardness, tensile, compression, bending, fatigue, etc. These tests are standardized and define the shape, dimensions, test speeds, machine calibration, accuracy of equipment, definition of characteristics, information to be included in a test report.
Tensile tests are very widely used in industry and they make it possible to know the tensile behaviour of materials, to determine their elastic behaviour, to understand the stress/strain relationship and to deduce from the test the attainable mechanical properties.
The tensile test gives several important values:
- the Young's modulus, E, or longitudinal modulus of elasticity, expressed in megapascals (MPa) or gigapascals (GPa);
- yield stress (when it exists), Re, σe, σy or fy (yield stress), which is used to characterize a conventional reversibility domain;
- the tensile strength Rm, σm or fu (ultimate limit), which defines the limit at rupture ;
- the elongation at break A%, which measures the capacity of a material to elongate under load before breaking, a property of interest in certain applications;
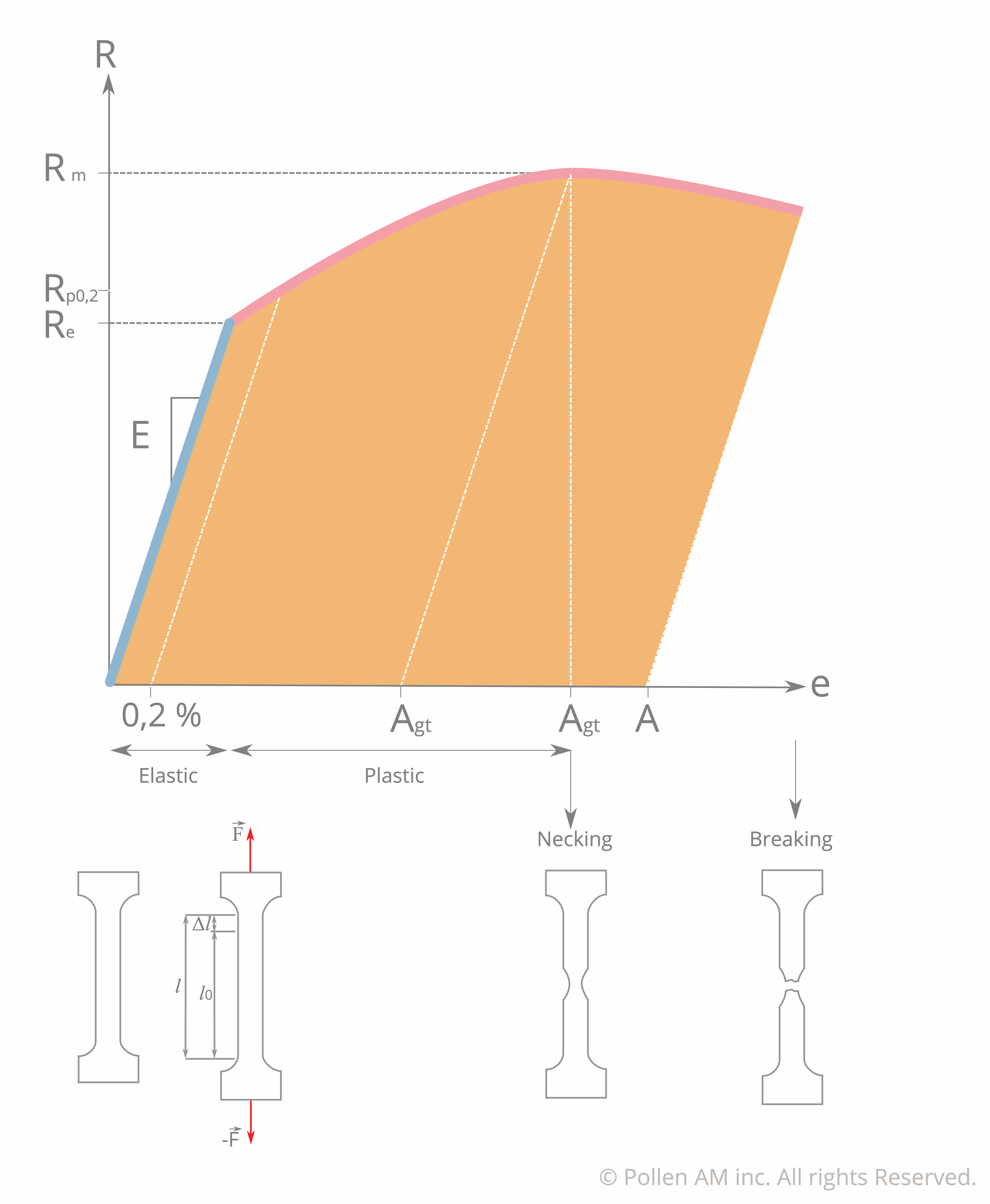
Melting-lamination temperature
In the thermomechanical analysis (TMA), the plastic deformation of a solid object is measured as a function of the temperature. During the measurement, a constant, usually low imposed load, acts on the test specimen. The measured deformation in the sample as a function of the temperature can be used among other things to determine the melting behaviour at a very low shear rate. This allows the melting temperature during thermal bonding processes to be deduced. The details of the measurement are stipulated in DIN EN ISO 11359-3.
Mesh
The mesh is the set of faces defining a 3D model.
During the 3D modelling phases, it is advisable to create a mesh with the maximum number of "quad" (composed of 4 vertices), when exporting to STL format, the model will be automatically converted to "sorting" (3 vertices).
Note that the quality of the export to STL file format impacts the final quality of the part. Indeed, it is sometimes necessary, especially for the production of parts with complex geometry, to maximize the number of polygons to avoid the facetizing of the part.
Micron
The micron is a reference unit of measurement. It is used, among other things, to express printing accuracy, layer height, etc.
Recall that 1 micron (1µm) = 0.001 millimetre, a precision of 100 microns is equal to 0.1 millimetre or one tenth.
Module-E
The modulus of elasticity (E-modulus) is determined by tensile tests on standard specimens. Defined according to DIN EN ISO 527-1A. The E-modulus corresponds to the ratio of a stress to the elastic deformation caused by this stress. The modulus of elasticity of plastics is influenced by the following parameters :
- temperature;
- moisture content ;
- orientation of macromolecules and loading rates;
- rate and duration of stress;
- specimen geometry ;
- type of test equipment.
N-gone
An N-Gon is a polygon with more than four vertices and edges. Because of its geometric properties, an N-Gon can always be divided into quads, triads or a combination of both, so they are always easy to remove by adding connecting edges between the vertices.
Needles
It is an accessory to clean, unblock the material outlet nozzles of the printer in case of blockage or plugging causing extrusion problems.
Pollen AM, offers needles to maintain the material outlet nozzles in Ø0.16mm and Ø.035mm.
NEMA
The National Electrical Manufacturers Association (or NEMA) is an American association created in 1926 by the merger of the Associated Manufacturers of Electrical Supplies and the Electric Power Club. This association brings together several manufacturers of electronic components worldwide and aims to define standards to ensure the intercompatibility of electronic systems between them.
These systems include stepper motors, which are widely used in the field of CNC machines and 3D printing.
They are referred to as NEMAxx, where "xx" is the dimension of the motor face in tenths of an inch. A NEMA17 will have a front face dimension of 1.7 x 1.7 inches, or 43.2 x 43.2 mm.
.
The Pam Series P and Pam Series M printers consist of 7 NEMA17 and 4 NEMA14 motors.
Nozzle
This is the part screwed to the end of the extruder heating element defining the diameter of the extruded wire. The nozzle diameter is a parameter impacting the accuracy of a print.
Pollen AM offers different material outlet nozzle diameters (Ø0.25; Ø0.40; Ø0.60; Ø0.80; Ø1.00 and Ø1.20 mm) as well as different alloys (brass, steel, other alloys are possible on request). Their geometry is specific and allows among others a self-centering of the nozzles in relation to the die of the extruder.
Do not confuse the material exit nozzle with the extruder.
Offset
An offset is a forced and voluntary shift of a measurement. For example, if an offset is applied to the Z axis of 1mm for example through the printer's control software, at the start of printing, the build plate will be offset from the nozzle by 1mm and this during the whole printing process.
The Pam Series P and Pam Series M printers allow X (abscissa axis) / Y (ordinate axis) / Z (depth axis) offset settings.
Offset Calibration (X/Y)
The X/Y offset calibration allows the different material outlet nozzles to be calibrated with each other.
X/Y calibration of extruders is particularly necessary in multi-extrusion applications. HoneyPrint, Pam's printer driver software, has a tab for editing this information.
Oozing
This is a printing defect due to too much pressure in the extruder causing small masses or drops to appear on the walls of the model.
To reduce this phenomenon, the extrusion temperature can be lowered and/or the shrinkage increased.
Over-extrusion
Over-extrusion occurs when the extruder deposits too much material. This generally unwanted phenomenon can degrade the quality of the part produced.
To avoid this, it will be necessary to adjust the flow rate/temperature ratio :
- The flow rate determines the speed of extrusion, the higher this value is, the faster the screw will rotate and therefore the greater the quantity of material deposited per unit of time. The flow rate is a multiplying coefficient expressed as a percentage and can take values higher than 100%. In cases of over-extrusion, it will probably be necessary to lower the value of the flow rate;
- adaptation of extrusion temperatures: reducing the extrusion temperature can also influence the amount of extruded material per unit of time. An extrusion temperature that is too high will make the material very fluid and will flow uncontrollably from the material outlet nozzle. By decreasing the extrusion temperature, the viscosity of the thermoplastic will increase and may reduce the flow rate.
Overhangs
Overhanging parts of a room often require a construction support to be printed. This sacrificial structure prevents these parts from sagging during printing.
All cantilevered parts do not require the use of a print medium. Pollen AM advises users of Pam technology to use a backing material when printing parts that are at an angle of less than 45° to the plane described by the build plate. Note, however, that the nature of the material also influences the use of the backing material.
Ozone resistance
The ozone molecule (O3) is formed by the union of three oxygen atoms. It is generated from reaction of oxygen in the atmosphere under the influence of high energy UV-radiation. Ozone is highly reactive, especially with organic substances. For example : Rubberbased elastomers are destroyed through cracking under the influence of ozone.
PA-12 - Material
Poyamide 12 is a semi-crystalline white industrial thermoplastic very similar to nylon 11 whose properties are generally slightly superior. Of all the unmodified generic nylons, it has lower values in water absorption rate, heat resistance and stress resistance. Compared with nylon 6 and 6.6, they both have a much lower water absorption rate (resulting in better electrical properties and better dimensional stability) and a higher cost. PA 12 is the ideal material for applications in the field of conveyor and drive technology such as wheels or pinions and precision industrial components requiring solidity at low temperatures.
PA-6 - Material
Polyamide-6 also called polycaprolactam, is a semi-crystalline thermoplastic. PA6 is used for the production of technical parts requiring good mechanical resistance. It has a low coefficient of friction, good thermal resistance and electrical insulation properties. It is widely used for gears, fittings and bearings, in the automotive industry for the underlying parts, and as a material for electrical boxes.
PA6-6 - Material
Polyamide-6-6 is a semi-crystalline thermoplastic and is the strongest unreinforced aliphatic nylon and the most resistant to abrasion and low temperatures. It has good resistance to friction and impact. PA6-6 can be alloyed with fiberglass or carbon and used as reinforcement materials.It is successfully used in various applications in the electronics, automotive, construction, and mining industries to manufacture mechanical parts, lubricant-free gears, fan blades, etc.
PBT - Material
PBT belongs to the family of polyesters. This semi-crystalline polymer has good electrical (insulating) properties, excellent heat resistance, good resistance to chemical agents. It is imperative to dry the material properly before processing.Widely used in applications with thermal and electrical constraints (contactor boxes, switches), in household appliances, etc.
PC - Material
PC (Polycarbonate) is a polymer with high transparency and is very resistant to impacts. This material is very rigid and has excellent mechanical properties that are characterized by low expansion and low heat distortion.Due to these properties, PC is mainly used for electrical and telecommunications applications, for example in the automotive industry.
PE - Material
Polyethylene is a semi-crystalline thermoplastic. Classified by its density and branching, PE properties depend of their molecular weight and structure. Ductile and impact resistant, it feels waxy when touched.Chemically stable it is a commodity thermoplastic widely used in packaging and film extrusion.
PEEK - Material
Polyetheretherketone (PEEK) is the most common and widely sold member of the polyaryletherketone family (PEAK). PEEK is a semi-crystalline thermoplastic with excellent mechanical and chemical resistance properties that are retained to high temperatures. It is highly resistant to thermal degradation, as well as to attack by both organic and aqueous environments.
PEEK is mainly used in medical & healthcare applications, automotive electrical & electronic, aerospace applications, Oil & gas, etc.
PEI - Material
Polyetherimide (PEI) material is an amorphous thermoplastic part of polyimides thermoplastics. Unfilled PEI thermoplastic is translucent and amber in color with exceptional mechanical, thermal and electrical properties.PEI plastic has similar characteristics to the polyarylsulphones (PSU, PPSU, PESU), while simultaneously offering significant advantages.PEI is mainly used for electrical and electronic applications, household appliances, aircraft interior design, automotive (under engine hood, interior parts, etc.), medical, etc.
PESU - Material
Polyethersulfone (PESU), is a high-performance material with a temperature profile that is unique among engineering thermoplastics a long-term temperature resistance up to 180°C.PESU is used in apparatus engineering and in the electrical and electronics fields in the automotive and transportation sectors, in the food and household sectors as a substitute for glass, metal, ceramic, and porcelain.
PET - Material
PET (polyethylene terephthalate) is a polyester used for the manufacture of plastic bottles, packaging or credit cards. PET is particularly used for its resistance.PET is a tough and sturdy material and a terrific alternative to PLA and ABS. It releases no fumes during printing and has very low shrinkage.
Pillowing
Cratering or pillowing is a defect that can appear on the top surfaces (top layers) of the printed part. Hollows or even holes are then visible. This phenomenon can be avoided by densifying the infill and/or by increasing the thickness of the top layer and/or by increasing the cooling of the cold spot 2, thus freezing the extruded material.
PLA Natural - Material
PLA (Polylactide acid) is an environmentally friendly biopolymer, made from renewable and recyclable resources. PLA accepts a wide variety of finishes: varnishing, polishing, painting, etc. With limited expansion and shrinkage properties, PLA is very suitable for printing precision parts as well as, in particular, for printing large sized objects with good dimensional stability.
PLA Woodfill - Material
PLA Woodfill is a bio composite that combines the printing qualities of PLA with excellent appearance properties. The PLA Woodfill gives the printed parts a unique charm and character. The PLA Woodfill accepts a wide variety of finishes: varnishing, polishing, painting, etc. This material is very appreciated producing decorative parts, designs, etc.
PMMA - Material
PMMA is an amorphous polymer with good balanced properties. Considered as a commodity thermoplastic, PMMA is mainly used for its optical transparency and elevated insulation properties (thermal, acoustic and electrical).Widely used for optics, households, automotive, lighting and medical applications.
Polar
Even rarer than the Cartesian and Delta type printers, a polar type 3D printer is based on the rotation of a build plate around an extrusion head, which can be compared to a pottery lathe. The manufacturing table also moves on the X (x-axis) / Y (y-axis) while the extrusion head moves on the Z (depth axis).
The Pam printers developed by Pollen AM are Delta type.
Polymer
A polymer is a macromolecule, that is, a large molecule composed of hundreds of monomers. Several families of polymers can be distinguished, such as thermosetting and thermoplastic polymers.
Pam technology is compatible with thermoplastic polymers in industrial granule form (thermoplastics and thermoplastic elastomers).
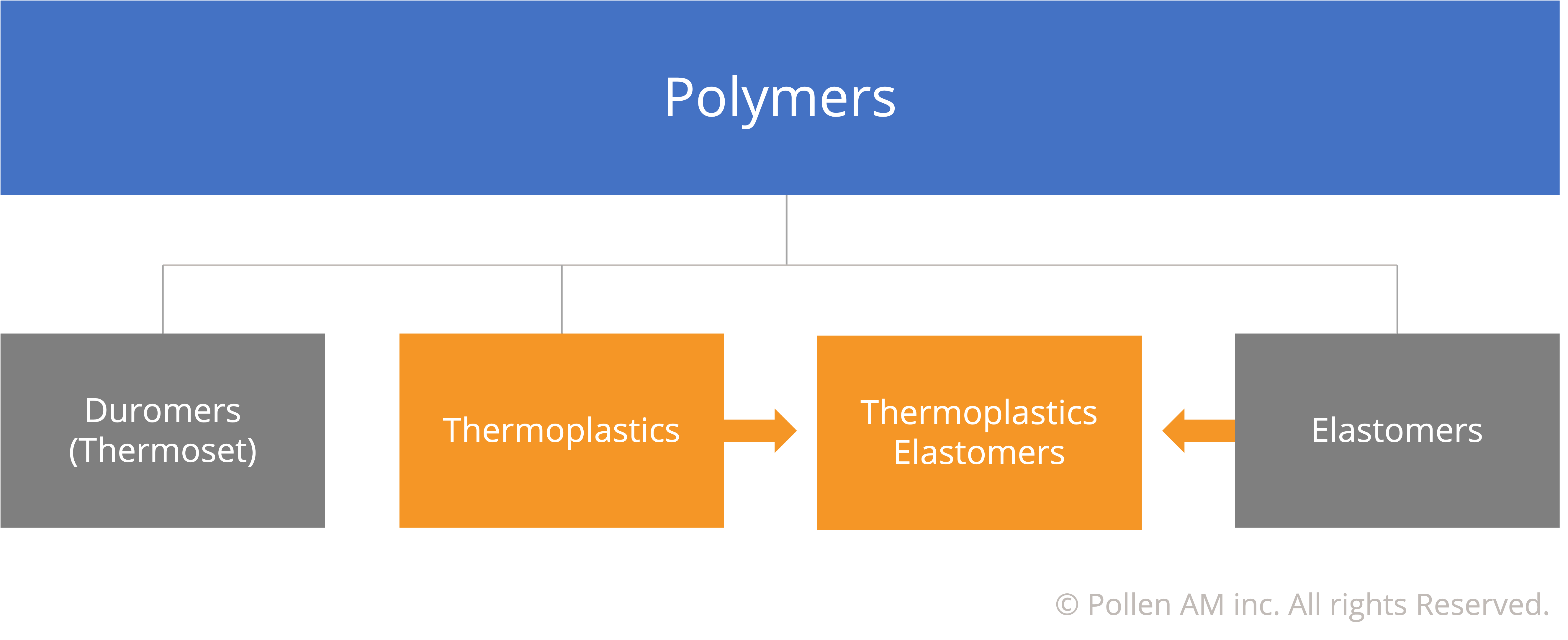
POM - Material
POM (polyoxymethylene) can withstand high mechanical stresses. POM is stiff, creep resistant, and withstands various stresses without warping. It has a low coefficient of friction, which gives it good wear resistance.
POM is commonly used for gears, shock components, friction components, electrical and electronics industry.
PP - Material
Polypropylene is a semi-crystalline thermoplastic. This material has a high level of flexibility, yet has great toughness meaning it is elastic without being too soft. PP is resistant to many chemicals and has a high resistance to electricity making it useful in electronic components.
PPS - Material
Polyphenylene sulfide (PPS) is a high-performance thermoplastic. Maximum service temperature is 218 °C. PPS has not been found to dissolve in any solvent at temperatures below approximately 200 °C.An easy way to identify the compound is by the metallic sound it makes when struck. PPS is used in filter for boilers, electrical insulation, capacitors, gaskets, and packing.
Print Head
Part of the printer (FDM) through which the filament exits. Once in the head, the material is heated by the heating body and exits in the molten phase through the material exit nozzle, also known as the nozzle.
Print profile
A print profile is a set of parameters that allow a part to be faithfully printed for a given material and given resolutions (material output nozzle, layer height, etc.). Changing a resolution parameter influences the print profile.
There are currently more than 400 print parameters.
Pollen AM has developed a print profile development protocol to quickly identify key setting pairs for a given material.
Print Speed
This is the speed of horizontal movement of the nozzle, measured in mm/s. The outer perimeter should generally be printed slower than the inner perimeters and infill (for a good finish a speed of 30mm/s is recommended).
Printing speed is a popular feature when buying a 3D printer. Indeed the design of a plastic part takes time, and the possibility to spend its printing time from 6h to 4h makes a difference.
Current printers have printing speeds ranging from 20mm/sec to 120mm/sec in standard speed. Some machines such as the Ultimaker 2 can push the printing up to 300mm/sec (however, you should not expect quality results at this speed).
Apart from the machine itself, the printing speed is affected by, among other things, the complexity of the workpiece or the desired precision.
Print Volume
Often referred to by the measurements "length x width x height" (or LxWxH), the print volume is the maximum volume of the object that can be printed by the 3D printer.
Pam systems have a manufacturing volume of Ø300 mm x H300 mm, i.e. a volume of 21,205,750 mm3.
Probe
The probe is a presence/distance sensor.
The Pam Series P and Pam Series M systems are equipped with a repositionable probe that allows you to map the manufacturing platform to correct flatness defects.
PTFE - Material
Polytetrafluoroethylene. Polymer with excellent thermal resistance as well as an extremely low coefficient of friction.
This is why this material was chosen to make the tube that allows the FEEDER filament to be fed to the extrusion head.
Quad
A quad or quadrilateral is a square or rectangular polygon with four sides. It has exactly 4 vertices at the corners connected by 4 edges. It is the most desired type of polygon when creating digital 3D models.
Radiant disc
The radiant disc is an accessory developed by Pollen AM. This local heating system (up to 300°C) keeps the last printed layers of the object being manufactured at temperature, improves interlayer adhesion, allows better management of the recrystallization of materials (semi-crystalline), limits the "bananage" effect, etc.
Combined with the manufacturing chamber (heated to a maximum of 70°C), an additional accessory allowing a thermally stable and homogeneous environment. The radiant plate is the key equipment, for the local thermal management of the materials during the manufacturing process, reducing shrinkage stresses and deformations during the crystallization phase.
Raft
The raft is a sacrificial piece made of several layers placed on the manufacturing tray. The part to be produced will be printed directly on the raft. The layers of the raft are generally thicker than the layers of the part to be produced and allow to optimize the adhesion of the part to be produced to the manufacturing plate limiting the warping phenomenon. Once printing is completed, the raft is removed from the final model.
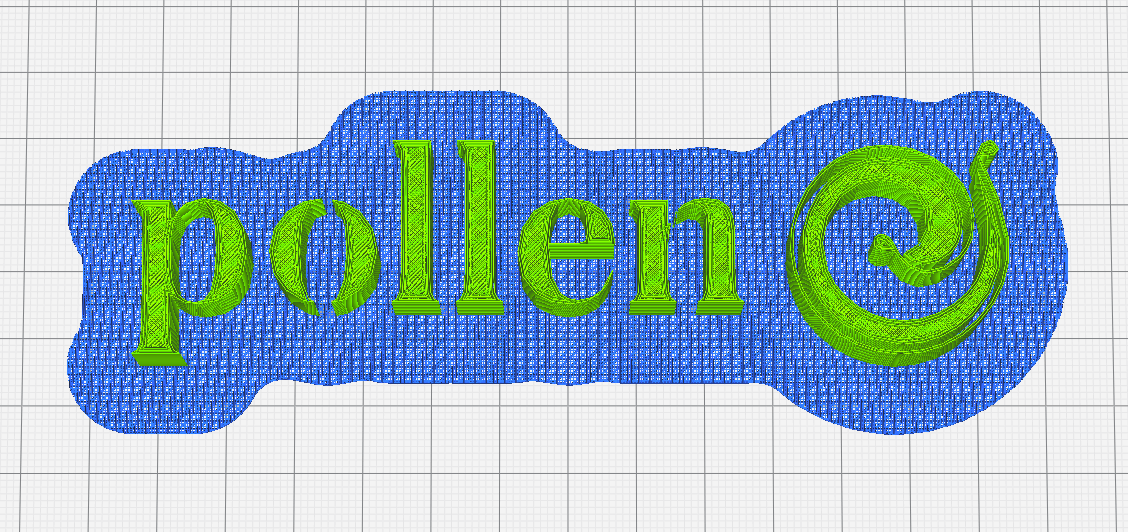
Scale
Scaling is a feature that allows you to resize a 3D object.
Scaling is expressed as a percentage or value. This function is available in most of the Cura software.
SD Card
An SD card ("SD" stands for Secure Digital) is a removable physical memory card for storing digital data. This medium was created in January 2000 by an alliance formed between the manufacturers Panasonic, SanDisk and Toshiba.
SD cards are traditionally used for storage and transmission of data between digital devices.
The systems developed by Pollen AM do not require this storage medium.
By default, Pam systems are shipped with the following network configuration:
- Ethernet: DHCP client
- The system is then used via a local connection from any client workstation to the machine connected on the same LAN as the 3D printer (computer, smartphone, tablet).
Shell
The shell is a category of parameter that defines the properties of an object to be printed. It is often associated with infill. The parameterization of these two values influences the mechanical resistance, the finish and the printing time.
A distinction is often made between the thickness of the vertical walls (shell) and that of the horizontal walls (top & bottom).
The thickness of the vertical walls must be a multiple of the diameter of the material outlet nozzle. (e.g. with a material outlet nozzle Ø0.4 mm a shell thickness of at least 0.8 mm is usually chosen).
The thickness of the horizontal walls should be a multiple of the layer thickness (with a layer thickness of 0.1 mm a Top and Bottom thickness of at least 0.4 mm is usually chosen).
Shore hardness
Shore hardness is a scale which aims to measure, among other things, the hardness of elastomers and certain plastics.
The measurement is based on the deformation of a spring according to a known displacement. There are several scales of shore hardness, the most well known of which are: Shore 00 (for extremely soft materials), Shore A (for medium soft materials) and Shore D (for harder materials).
Unlike filaments that have difficulty printing soft materials, the technology developed by Pollen AM has no limits in printing soft materials. Pam's technology is capable of printing flexible materials from Shore00 to ShoreD.
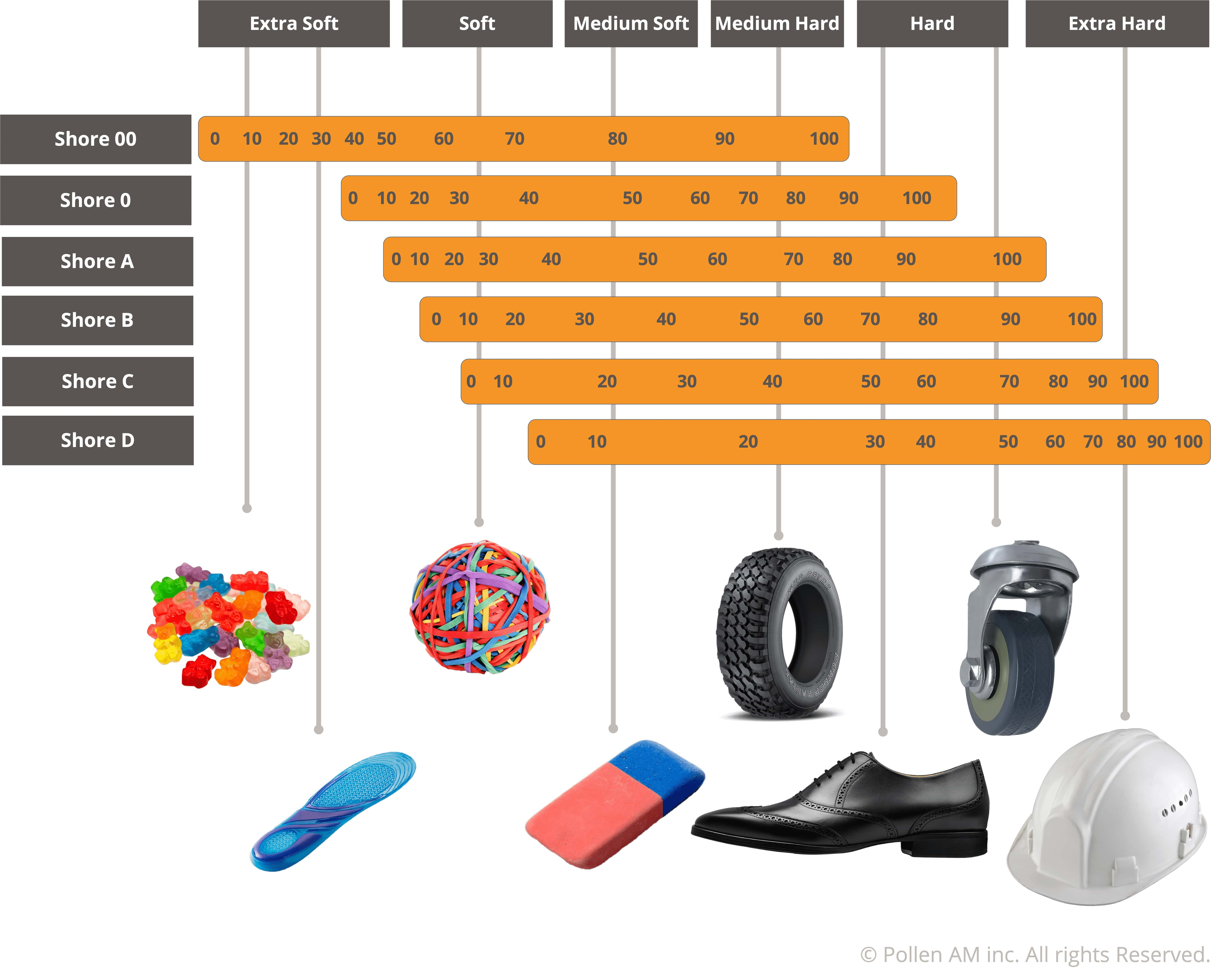
Shrinking
When the build plate moves during the production cycle and no material is deposited on the workpiece, the extruder performs a retraction. Pam systems retract by reverse rotation of the extruder screw.
Retractions limit the stringing phenomenon.
Skirt
The skirt defines an initial deposit of material around the part to be printed. The skirt is deposited before the production of the part to ensure a regular flow and to purge the material outlet nozzle one last time before starting the printing process.
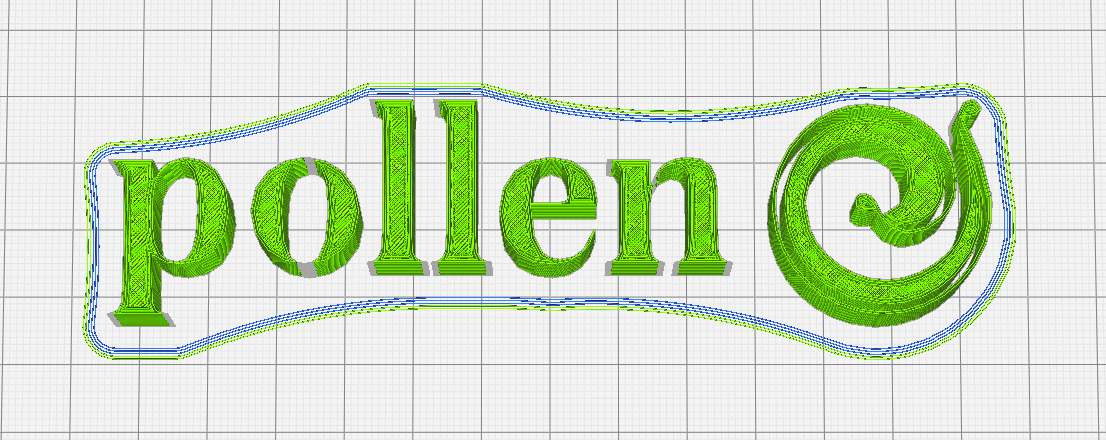
Slicer
This is the software that will slice a 3D model into thin horizontal layers in order to give instructions to the printer.
Pollen AM uses Cura software.
Stringing
Stringing is a printing defect that generates unwanted threads between different parts of a printed part. This phenomenon can be reduced by increasing the retraction length and/or accelerating the speed of the build plate movement when the print head is not extruding and/or by lowering the extrusion temperature.
Support structure
The support structure are additions of soluble materials allowing you to print cantilevered parts on your parts. In the case of a figure with the arms spread apart, the first layer deposited to form the arms will not rest on anything if the supports are absent; your extruder will therefore deposit filaments in a vacuum.
From 30° of inclination, the supports are generally necessary.
The support materials are PVA (soluble in water and recommended with PLA), and HIPS (soluble in D-limonene and recommended with ABS).
Surface resistivity
The specific surface resistance is the resistance of the surface of a test piece. It is measured between two electrodes of dimensions prescribed in DIN EN 62631-3-2, fixed to the surface at a specified distance.
Swelling
The suitability of a plastic for a particular application often depends on its resistance to chemicals. Swelling is the fundamental physical process of the absorption of liquid substances by a solid. In this process, the substance enters into the material without chemical interaction between the substance and the plastic. This results in an increase in volume and weight with a corresponding reduction in mechanical values. After evaporation, a reduction in swelling occurs and the original properties of the product are almost completely restored. Thus, swelling is a reversible process.
PVA - Material
PVA (Polyvinyl Alcohol) is a water-soluble support material. It is used to print support structures when producing cantilever parts. Depending on the materials and angles of inclination, it becomes necessary to use support brackets to maintain stability and good performance of the printed part. PVA is sensitive to moisture and heat.
Tear strength
Tear strength is the term which defines the resistance of a notched test specimen to tear propagation.
The test is conducted in accordance with DIN ISO 34–1Bb using an angle specimen with cut. The tear resistance [kN/m] is the ratio between maximum force and specimen thickness.
Teflon tape
Teflon tape is an indispensable consumable to improve the tightness of the material outlet nozzle assembly in the extrusion die.
Thermal deformation
Various tests can be used to compare the application limits of plastics at increased temperature. These include the determination of the Vicat Softening Temperature (VST) according to ISO 306 and the determination of the Heat Deflection Temperature (HDT) according to ISO 75.
Thermal expansion
As all materials, thermoplastics are subject to a temperature dependent, reversible variation in length. This is defined by the coefficient of linear expansion α [1/K] in relation to temperature and determined in accordance with ISO 11359-1-2. The influence of temperature is obvious and has to be considered for many applications.
Thermistor
Temperature measuring probe at the heating element of an FDM 3D printer.
Thermoplastic
Thermoplastic means a material that repeatedly softens when heated above a certain temperature, but becomes hard again once the material has cooled.
Pam's technology uses pelletized thermoplastics to produce parts.
Torsion modulus
The torsional vibration test as specified in DIN EN ISO 6721-2 is used to determine the elastic behaviour of polymeric materials under dynamic torsional loading over a temperature range. In this test, a test specimen is stimulated in free torsional vibration. The torsion angle is kept sufficiently low to avoid permanent deformation. According to the test parameters specified in the standard, a frequency of 0.1 to 10 Hz results when the temperature rises.
During the relaxation phase, the decreasing sinusoidal vibration is recorded. From this decay curve it is possible to calculate the torsional modulus and the damping. The torsional modulus is the ratio between the torsional stress and the resulting elastic angular deformation.
Tri
A triangular polygon is called a tri or triangle and is a simple polygon with three sides. It has exactly 3 vertices at its corners and 3 edges connecting these points. This is the smallest configuration required to create a polygonal face. STL file formats are made up of sorts.
Under extrusion
This is a printing defect that occurs when the filament flow is not sufficient. This results in holes in some layers or hollows between layers.
This insufficient flow can come from printing conditions at the limit of what the printer can deliver (above 10mm3/s). In this case, the feeder pushes harder and harder on the filament and finally releases this pressure by making a sound " clack " (this is a safety device to prevent the feeder from nibbling the filament). In this case it is therefore necessary to review the printing parameters to avoid creating too extreme conditions.
This problem can unfortunately have many causes: partially clogged nozzles, extrusion temperature too low, incorrectly adjusted feeder, too thick or irregularly thick filaments, end of coil, combing, etc.
In any case you should not increase the filament flow, contrary to what you might think, it does not bring anything good.
UV radiation
Plastics are chemically degraded by the effect of UV radiation. The degree of ageing depends on duration and intensity. It is possible to improve UV resistance by addition of color pigments which prevent the deep penetration of UV rays and thus mechanical destruction. Moreover, dark color shades, in particular black, mask the surface discoloration. The ageing process can also be delayed by the addition of UV stabilizers. Suitable master batches are available.
Vase mode
This is a printing mode in which the Z-axis does not move smoothly at the end of each layer. It moves progressively throughout the printing process, it is also said to be a dynamic 'Z'.
Vase printing is very restrictive on the characteristics of the model to be printed, but generally allows cleaner prints.
Vector
3D models are vector files. They represent a series of vectors that form polygons.
The set of its polygons represent the 3D model. The points connecting the vectors are vertices.
Vicat softening temperature
In the course of this test, a loaded needle (Vicat A: 10 N, Vicat B: 50 N) with a diameter of 1 mm2 is placed on a test specimen, which is located on a plane surface within a temperature transfer medium. The temperature of the medium (oil or air) is increased at a constant heating rate (50 K/h or 120 K/h). The VST is the temperature at which the needle penetrates by 1 mm into the test material.
VOC
Volatile organic compounds, or VOCs, are organic compounds that can easily be found in the atmosphere in gaseous form. The processing of thermoplastics can lead to the release of VOCs, which, among other things, is synonymous with particular odours. It should be noted that some could be very dangerous to health.
Specifically, these are nanoparticles (diameter less than 100 nm), particles with diameters ranging from 200 to 500 nm and traces of additives. Their composition varies according to the materials used.
As an option, Pollen AM offers filter boxes to limit the amount of VOCs released during the polymer conversion process.
Volume resistivity
Volume resistivity as defined in DIN EN 63631-3-1 is the electrical resistance of the bulk material measured between two electrodes, relative to the geometry of the test piece. The type of electrode arrangement makes it possible to ignore surface resistance.
Water Vapour Permeability
The water vapour permeability (WDD) [g / (m2 · d)] of a plastic is determined in accordance with the DIN 53122-1 standard. It is defined as the amount of water vapour passing through 1 m2 of test specimen under defined conditions (temperature, differential humidity) within 24 hours, and is approximately in inverse proportion to the thickness of the specimen.
Warping
Warping is a printing defect resulting in a deformation, more or less important depending on the materials. This phenomenon often occurs at the corners of the part and is related to the cooling or shrinkage of the thermoplastic.
Several parameters, accessories and equipment can help to reduce this effect, such as:
- use of a micro-perforated printing plate;
- setting of the temperature of the manufacturing tray ;
- use of a heating chamber and / or a radiant panel ;
- use of specific tray adhesion films;
- printing of a raft or raft in French;
- printing a brim, etc.
XML - eXtensible Markup Language
XML or eXtensible Markup Language is a computer language of description. This computer language does not require technical knowledge of coding to be used.
As it is naturally structured, it is easy to read and understand. This language is accessible without any specific code editing software to write it, a simple word processing software is sufficient. It is universal, i.e. it does not encounter any compatibility problems with other technologies.
Finally, it is extensible, it is possible to add new tags as needed. The XML file format is the basis of several file formats used in 3D printing, such as 3MF and AMF.
Z-OFFSET
This is the OFFSET on the Z axis, often referred to as the Z-axis OFFSET. See OFFSET.